HDPE (high-density polyethylene) double-wall corrugated pipe
A double-wall corrugated pipe and pipe technology, applied in the field of plastic pipes, can solve the problems of mechanical properties, impact resistance deformability, poor anti-aging performance and anti-fouling performance, etc., to improve mechanical properties, improve mechanical properties, and thermal deformation. The effect of temperature increase
- Summary
- Abstract
- Description
- Claims
- Application Information
AI Technical Summary
Problems solved by technology
Method used
Examples
Embodiment 1
[0081] A HDPE double -wall ripple tube, which includes the raw material component of the following quality portion:
[0082] HDPE 50 copies
[0083] LDPE 18 copies
[0084] LLDPE 20 copies
[0085] 16 polypropylene
[0086] Monte 10 parts
[0087] 12 parts of white charcoal black
[0088] 5 sulfate
[0089] 25 parts of oxide graphene
[0090] 20 copies of carbon nanotin
[0091] 25 copies of polytamide fiber
[0092]Silicane coupling agent KH 570 5 parts
[0093] N-methylpinol 4 parts
[0094] 10 copies of composite lubricant
[0095] Titanium dioxide 10 part
[0096] Nano -silver 0.2 part
[0097] 5 parts of catechins
[0099] 5 parts of polyacrylamide
[0100] 10 copies of mannitol
[0101] 10 copies of methyl etchylite
Embodiment 2
[0104] A HDPE double -wall ripple tube, which includes the raw material component of the following quality portion:
[0105] HDPE 10
[0106] LDPE 3
[0107] Lldpe 8
[0108] 10 parts of polypropylene
[0109] Monte soil 5 copies
[0110] White charcoal and black 5 copies
[0111] 1 portal of sulfate
[0112] 15 parts of oxide graphene
[0113] 10 copies of carbon nanotubes
[0114] 10 parts of polyiline fiber
[0115] Silicine coupling KH 570 0.5 part
[0116] N-methylpinol 1 copy
[0117] 1 copy of the composite lubricant
[0118] Titanium dioxide 5 part
[0119] Nano -silver 0.01 copies
[0120] 儿 儿 0.5 part
[0121] Calcium calcium 0.5 part
[0122] 1 part of polyacrylamide
[0123] 5 copies of mannitol
[0124] Five copies of methampitromyate
[0125] Peroxidine hydrates 1 part.
Embodiment 3
[0127] A HDPE double -wall ripple tube, which includes the raw material component of the following quality portion:
[0128] HDPE 40 copies
[0129] LDPE 12
[0130] LLDPE 16 copies
[0131] 14 copies of polypropylene
[0132] Mongolian Earth 8
[0133] 10 copies of white carbon black
[0134] 4 sulfate
[0135] 22 graphene oxide
[0136] 18 parts of carbon nanotin
[0137] 20 parts of polyiline fiber
[0138] Silicane coupling agent KH 570 4 part
[0139] N-methylpinol 3 parts
[0140] 8 parts of composite lubricant
[0141] Titanium dioxide 8 part
[0142] Nano -silver 0.1 part
[0143] 4 parts of catechins
[0144] Calcium calcium 3 part
[0145] 4 parts of polyacrylamide
[0146] 8 copies of mannitol
[0147] 8 copies of methylicate
[0148] 4 parts of oxide oxide
PUM
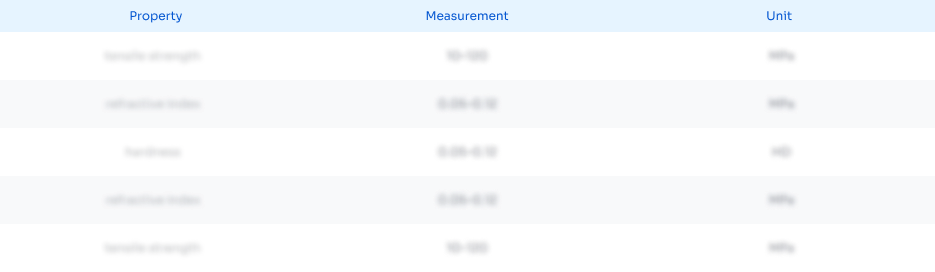
Abstract
Description
Claims
Application Information

- R&D
- Intellectual Property
- Life Sciences
- Materials
- Tech Scout
- Unparalleled Data Quality
- Higher Quality Content
- 60% Fewer Hallucinations
Browse by: Latest US Patents, China's latest patents, Technical Efficacy Thesaurus, Application Domain, Technology Topic, Popular Technical Reports.
© 2025 PatSnap. All rights reserved.Legal|Privacy policy|Modern Slavery Act Transparency Statement|Sitemap|About US| Contact US: help@patsnap.com