Method for preparing silver tin oxide contact materials by high pressure oxidation of alloy powder ingots
A technology of silver tin oxide and contact materials, which is applied in the direction of cable/conductor manufacturing, electrical components, circuits, etc., can solve the problems of unstable electrical performance, affecting electrical life, and poor oxide areas, so as to ensure uniformity of structure, Effects of improving processability and improving sintering strength
- Summary
- Abstract
- Description
- Claims
- Application Information
AI Technical Summary
Problems solved by technology
Method used
Image
Examples
Embodiment 1
[0021] 1) Weigh 17.6kg of pure silver block, 1.80kg of pure tin block, 0.048kg of pure copper block and 0.050kg of pure indium block, put them into an intermediate frequency furnace for melting (melting temperature is 1250°C), and then pass through high-pressure water atomization equipment Carrying out atomization, drying the obtained powder slurry, and passing through a 200-mesh sieve to obtain silver-tin alloy powder;
[0022] 2) The obtained silver-tin alloy powder is placed in an isostatic press to make a cylindrical ingot of φ85m×380mm under a pressure of 130MPa;
[0023] 3) The obtained ingot is placed in a nitrogen atmosphere and pre-sintered at 700°C for 3 hours to obtain a pre-sintered ingot;
[0024] 4) The obtained pre-sintered ingot is oxidized in an oxygen-containing atmosphere to obtain an oxidized ingot; the process parameters of the oxidation are: pressure 0.6MPa, temperature 850°C, time 4h;
[0025] 5) The obtained oxidized ingot is sintered in a sintering fu...
Embodiment 2
[0034] 1) Weigh 17.6kg of pure silver block, 1.80kg of pure tin block, 0.048kg of pure copper block and 0.054kg of pure bismuth block, put them into an intermediate frequency furnace for melting (melting temperature is 1250°C), and then pass through high-pressure water atomization equipment Carrying out atomization, drying the obtained powder slurry, and passing through a 100-mesh sieve to obtain silver tin oxide powder;
[0035] 2) The obtained silver tin oxide powder is placed in an isostatic press to make a cylindrical ingot of φ80m×380mm under a pressure of 100MPa;
[0036] 3) The obtained ingot is placed in an argon atmosphere and pre-sintered at 600°C for 5 hours to obtain a pre-sintered ingot;
[0037] 4) The obtained pre-sintered ingot is oxidized in an oxygen-containing atmosphere to obtain an oxidized ingot; the process parameters of the oxidation are: pressure 0.8MPa, temperature 800°C, time 5h;
[0038] 5) The obtained oxidized ingot is sintered in a sintering fur...
Embodiment 3
[0041] 1) Weigh 17.6kg of pure silver block and 1.89kg of pure tin block respectively, put them into an intermediate frequency furnace for melting (melting temperature is 1250°C), and then atomize through high-pressure water atomization equipment, and dry the obtained powder slurry , through a 200-mesh sieve to obtain silver tin oxide powder;
[0042] 2) The obtained silver tin oxide powder is placed in an isostatic press to make a cylindrical ingot of φ85m×380mm under a pressure of 150MPa;
[0043] 3) The obtained ingot is placed in a nitrogen atmosphere and pre-sintered at 750° C. for 4 hours to obtain a pre-sintered ingot;
[0044]4) The obtained pre-sintered ingot is oxidized in an oxygen-containing atmosphere to obtain an oxidized ingot; the process parameters of the oxidation are: pressure 0.5MPa, temperature 850°C, time 3h;
[0045] 5) The obtained oxidized ingot is sintered in a sintering furnace, the sintering temperature is controlled to be 880° C., and the sinterin...
PUM
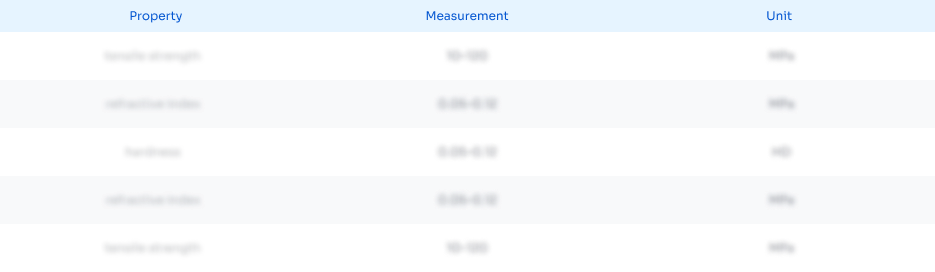
Abstract
Description
Claims
Application Information

- R&D
- Intellectual Property
- Life Sciences
- Materials
- Tech Scout
- Unparalleled Data Quality
- Higher Quality Content
- 60% Fewer Hallucinations
Browse by: Latest US Patents, China's latest patents, Technical Efficacy Thesaurus, Application Domain, Technology Topic, Popular Technical Reports.
© 2025 PatSnap. All rights reserved.Legal|Privacy policy|Modern Slavery Act Transparency Statement|Sitemap|About US| Contact US: help@patsnap.com