Process for synthesis of polyoxymethylene dimethyl ether from methyl
A technology of polyoxymethylene dimethyl ether and process method, which is applied in the technical field of synthesizing polyoxymethylene dimethyl ether from methanol, can solve the problems of high cost and low yield of synthetic process products, achieve high yield and selectivity, and convenient operation , the effect of low production cost
- Summary
- Abstract
- Description
- Claims
- Application Information
AI Technical Summary
Problems solved by technology
Method used
Image
Examples
Embodiment 1
[0029] Fill 150g in fixed-bed reactor 5, silver-silica-alumina catalyst (composed of silver, silicon oxide and aluminum oxide in mass fraction ratio 18:75:7), fill 150g HZSM-5 molecular sieve (Si / Al=15), purging the device with nitrogen, the liquid phase methanol is heated, vaporized and mixed with air to feed the fixed bed reactor, the air volume space velocity is 4500h -1 , the feed rate of methanol is 93.75g / h, the operating temperature of the fixed-bed reactor is 600°C, and the pressure is 1MPa; at the same time, recycle anhydrous methanol and polyoxymethylene dimethyl ether (n= 1, 2, 5, 6) for the mixed solution, the feed rate is 62.5g / h and 109g / h respectively. The operating conditions of the bubble reactor 7 are a reaction temperature of 150° C. and a reaction pressure of 3.0 MPa. The reaction output enters the anion exchange resin bed layer.
[0030] The discharge material 9 of the bubbling reactor 7 passes through the anion exchange resin bed 10 to remove acid, and...
Embodiment 2
[0032] Fill 150g in the fixed-bed reactor 5, molybdenum-iron catalyst (composed of molybdenum oxide and iron oxide molar ratio 2.00:1), fill 300g strongly acidic styrene-based cation exchange resin in the bubble reactor 7, blow with nitrogen Sweeping device, the liquid phase methanol is heated, vaporized and mixed with air, and then fed to the fixed bed reactor, the air volume space velocity is 4500h -1 , the feed rate of methanol is 93.75g / h, the operating temperature of the fixed-bed reactor is 380°C, and the pressure is 1MPa; at the same time, recycle anhydrous methanol and polyoxymethylene dimethyl ether (n= 1, 2, 5, 6) for the mixed solution, the feed rate is 93.75g / h and 85.5g / h respectively. The operating conditions of the bubble reactor 7 were a reaction temperature of 110°C and a reaction pressure of 1.0 MPa. The reaction output enters the anion exchange resin bed layer.
[0033] Other operations are the same as in Example 1, continuous reaction for 80h, online samp...
Embodiment 3
[0035] Fill 150g in fixed-bed reactor 5, ferromolybdenum catalyst (composed of molybdenum oxide and iron oxide molar ratio 1.90:1), fill 300g dinitrobenzoic acid in bubble reactor 7, purging device with nitrogen, The liquid phase methanol is heated, vaporized and mixed with air, and then fed to the fixed bed reactor, the air volume space velocity is 4500h -1 , the feed rate of methanol is 93.75g / h, the operating temperature of the fixed-bed reactor is 380°C, and the pressure is 1MPa; at the same time, recycle anhydrous methanol and polyoxymethylene dimethyl ether (n= 1, 2, 5, 6) for the mixed solution, the feed rate is 93.75g / h and 106.1g / h respectively. The operating conditions of the bubble reactor 7 are a reaction temperature of 110° C. and a reaction pressure of 1.0 MPa. The reaction output enters the anion exchange resin bed layer.
[0036] Other operations are the same as in Example 1, continuous reaction for 80h, online sampling of the product, analysis by gas chromat...
PUM
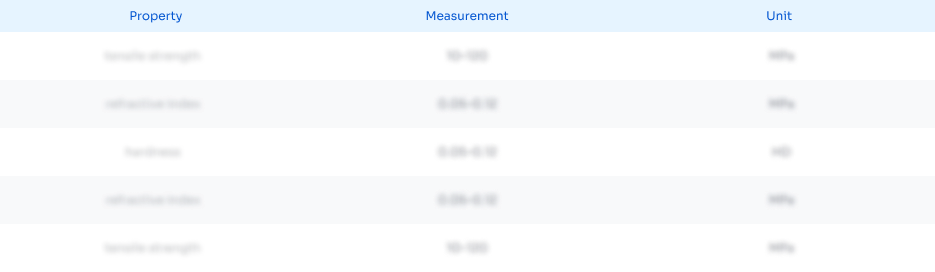
Abstract
Description
Claims
Application Information

- R&D
- Intellectual Property
- Life Sciences
- Materials
- Tech Scout
- Unparalleled Data Quality
- Higher Quality Content
- 60% Fewer Hallucinations
Browse by: Latest US Patents, China's latest patents, Technical Efficacy Thesaurus, Application Domain, Technology Topic, Popular Technical Reports.
© 2025 PatSnap. All rights reserved.Legal|Privacy policy|Modern Slavery Act Transparency Statement|Sitemap|About US| Contact US: help@patsnap.com