Alloy material liquid forging release agent and preparing method thereof
A liquid die forging, alloy material technology, applied in metal processing equipment, manufacturing tools, casting and molding equipment, etc., can solve the problems affecting the process yield and secondary processing operations, unenvironmental operator health, and high organic matter volatility. Achieve the effect of preventing the mold temperature from passing out too quickly, improving the suspension, and increasing the softening temperature
- Summary
- Abstract
- Description
- Claims
- Application Information
AI Technical Summary
Problems solved by technology
Method used
Examples
Embodiment 1
[0026] A liquid die forging release agent for alloy materials, which is made of the following components by weight percentage: mullite 6%; talc powder 1%; light silicon dioxide 0.5%; diatomite 1%; Sodium polycarboxylate 0.5%; Isomerized tridecyl alcohol polyoxyethylene ether 0.1%; Sodium polyacrylate 0.05%; N-octanoic acid 0.05%; N-capric acid 0.05%; Magnesium hydrogen phosphate trihydrate 0.02%; Oxyethylene ether phosphate potassium salt 0.05%; polyether silicone 0.5%; dialkyl sulfosuccinate 0.01%; the balance is deionized water.
[0027] Its preparation method comprises the following steps in turn:
[0028] a. Add isomeric tridecyl alcohol polyoxyethylene ether, polyether silicone, polyoxyethylene ether phosphate potassium salt, n-octanoic acid, and n-decanoic acid to water in sequence, and then stir for 0.5 hours to obtain a mixed solution;
[0029] b. Use a high-speed emulsifier to emulsify the mixed solution obtained in step a until it is uniform. The emulsification time...
Embodiment 2
[0035] A liquid die forging release agent for alloy materials, which is made of the following components by weight percentage: 18% mullite; 5% talc; 5% light silicon dioxide; 5% diatomaceous earth; Sodium polycarboxylate 1%; Isomerized tridecanol polyoxyethylene ether 1.5%; Sodium polyacrylate 0.1%; N-octanoic acid 1.5%; N-decanoic acid 1.5%; Magnesium hydrogen phosphate trihydrate 0.6%; Gum Arabic 1.5%; Oxyethylene ether phosphate potassium salt 0.8%; polyether silicone 1.5%; dialkyl sulfosuccinate 0.3%; the balance is deionized water.
[0036] Its preparation method comprises the following steps in turn:
[0037] a. Add isomeric tridecyl alcohol polyoxyethylene ether, polyether silicone, polyoxyethylene ether phosphate potassium salt, n-octanoic acid, and n-decanoic acid to water in sequence, and then stir for 1 hour to obtain a mixed solution;
[0038] b. Emulsify the mixed solution obtained through step a until uniform with a high-speed emulsifier, and the emulsification ...
Embodiment 3
[0044] A liquid mold release agent for alloy materials, which is made of the following components by weight percentage: 10% of mullite; 3% of talc; 2.5% of light silicon dioxide; 3% of diatomite; Sodium polycarboxylate 0.7%; Isomerized tridecanol polyoxyethylene ether 0.9%; Sodium polyacrylate 0.08%; N-octanoic acid 1.2%; N-decanoic acid 1.4%; Magnesium hydrogen phosphate trihydrate 0.35%; Gum Arabic 0.7%; Oxyethylene ether phosphate potassium salt 0.6%; polyether silicone 1.2%; dialkyl sulfosuccinate 0.15%; the balance is deionized water.
[0045] Its preparation method comprises the following steps in turn:
[0046] a. Add isomeric tridecyl alcohol polyoxyethylene ether, polyether silicone, polyoxyethylene ether phosphate potassium salt, n-octanoic acid, and n-decanoic acid to water in sequence, and then stir for 0.8 hours to obtain a mixed solution;
[0047] b. Emulsify the mixed solution obtained through step a until uniform with a high-speed emulsifier, and the emulsific...
PUM
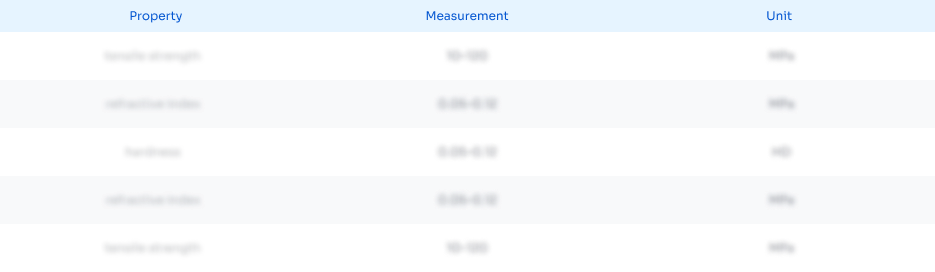
Abstract
Description
Claims
Application Information

- R&D Engineer
- R&D Manager
- IP Professional
- Industry Leading Data Capabilities
- Powerful AI technology
- Patent DNA Extraction
Browse by: Latest US Patents, China's latest patents, Technical Efficacy Thesaurus, Application Domain, Technology Topic, Popular Technical Reports.
© 2024 PatSnap. All rights reserved.Legal|Privacy policy|Modern Slavery Act Transparency Statement|Sitemap|About US| Contact US: help@patsnap.com