Manufacturing method of tin-copper double-layer electroplated steel plates
A manufacturing method and technology for steel plates, which are applied in the field of manufacturing tin-copper double-layer electroplated steel plates, can solve the problems of poor welding performance of galvanized layers, affecting the processing performance and corrosion resistance of steel plates, etc.
- Summary
- Abstract
- Description
- Claims
- Application Information
AI Technical Summary
Problems solved by technology
Method used
Image
Examples
Embodiment 1
[0018] The ultra-thin cold-rolled steel sheet with a specification of 150×100×0.18mm is first derusted, washed, activated with dilute acid, and then dipped in nickel-containing solution. The formula of the nickel-impregnated solution is: nickel sulfate (NiSO 4 ·6H 2 O)): 30g / L, sodium hypophosphite (NaH 2 PO 2 ·H 2 O): 10g / L, sodium acetate (NaAc·3H 2 O) 10g / L, pH value: 4~6, temperature: 90°C, immersion nickel amount 30~50mg / m 2 , and then wash with water;
[0019] Copper is electroplated on the surface again, and the formula of electroplating copper solution is composed of: copper pyrophosphate (Cu 2 P 2 o 7 ): 65g / L, potassium pyrophosphate (K 4 P 2 o 7.. 3H 2 O): 230g / L, ammonia water: 2mL / L, DK-105 brightener 1mL / L, P 比 (P 2 o 7 4- / C u 2+ ):6.40~7.0, pH value 8.6~9.0, temperature: 50°C, cathode current density: 3A / dm2, anode: oxygen-free electrolytic copper plate, copper plating amount: 1.0 g / m2, copper plating will be finished with water After the surf...
Embodiment 2
[0021] The ultra-thin cold-rolled steel sheet with a specification of 150×100×0.25mm is first derusted, washed, activated with dilute acid, and then dipped in nickel-containing solution. 4 ·6H 2 O)): 30g / L, sodium hypophosphite (NaH 2 PO 2 ·H 2 O): 10g / L, sodium acetate (NaAc·3H 2 O) 10g / L, pH value: 4~6, temperature: 90°C, immersion nickel amount 30~50mg / m 2 , and then wash with water;
[0022] Copper is electroplated on the surface again, and the formula of electroplating copper solution is composed of: copper pyrophosphate (Cu 2 P 2 o 7 ): 95g / L, potassium pyrophosphate (K 4 P 2 o 7.. 3H 2 O): 280g / L, ammonia water: 3mL / L, DK-105 brightener 2mL / L, P 比 (P 2 o 7 4- / C u 2+ ):6.4~7.0, pH value 8.6~9.0, temperature: 55°C, cathode current density: 8A / dm2, anode: oxygen-free electrolytic copper plate, copper plating amount: 1.5g / m2, copper plating will be finished with water After the surface of the thin steel plate is cleaned, it is immediately put into an elec...
Embodiment 3
[0024] The ultra-thin cold-rolled steel sheet with a specification of 150×100×0.3mm is first derusted, cleaned, activated with dilute acid, and first dipped in nickel-containing solution. The formula of the nickel-impregnated solution is: nickel sulfate (NiSO 4 ·6H 2 O)): 30g / L, sodium hypophosphite (NaH 2 PO 2 ·H 2 O): 10g / L, sodium acetate (NaAc·3H 2 O) 10g / L, pH value: 4~6, temperature: 90°C, immersion nickel amount 30~50mg / m 2 , and then wash with water;
[0025] Copper is electroplated on the surface again, and the formula of electroplating copper solution is composed of: copper pyrophosphate (Cu 2 P 2 o 7 ) 105g / L, potassium pyrophosphate (K 4 P 2 o 7.. 3H 2 O): 370g / L, ammonia water: 5mL / L, DK-105 brightener 3mL / L, P 比 (P 2 o 7 4- / C u 2+ ):6.4~7.0, pH value 8.6~9.0, temperature: 60℃, cathode current density: 7A / dm2, anode: anaerobic electrolytic copper plate, copper plating amount: 2.5g / m2, copper plating will be finished with water After the surface ...
PUM
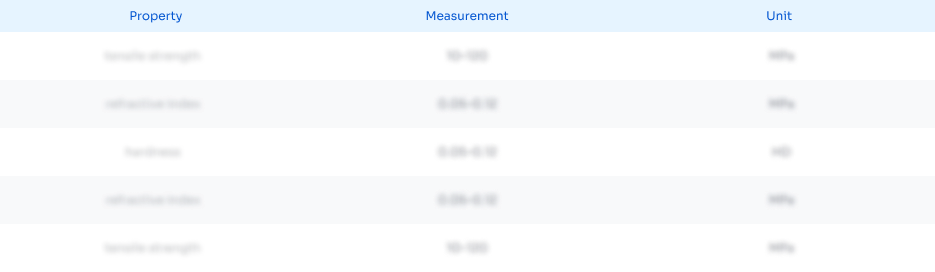
Abstract
Description
Claims
Application Information

- R&D Engineer
- R&D Manager
- IP Professional
- Industry Leading Data Capabilities
- Powerful AI technology
- Patent DNA Extraction
Browse by: Latest US Patents, China's latest patents, Technical Efficacy Thesaurus, Application Domain, Technology Topic, Popular Technical Reports.
© 2024 PatSnap. All rights reserved.Legal|Privacy policy|Modern Slavery Act Transparency Statement|Sitemap|About US| Contact US: help@patsnap.com