Preparation method and application of three-element siloxane sponge
A siloxane sponge and siloxane technology, applied in the direction of separation methods, chemical instruments and methods, grease/oily substances/floating matter removal devices, etc., can solve the problems of low mechanical properties and achieve low density and fast oil absorption speed , the effect of fast absorption rate
- Summary
- Abstract
- Description
- Claims
- Application Information
AI Technical Summary
Problems solved by technology
Method used
Image
Examples
Embodiment 1
[0028] a. Hydrolysis of alkoxysilane to form a sol: 6.0g (0.0165mol) of cetyltrimethylammonium bromide was added to 130mL (7.2222mol) of sulfuric acid solution with pH = 2, and then 1.0g (0.0048mol) was added successively ) Tetraethoxysilane, 14g (0.1028mol) methyltrimethoxysilane, 31g (0.2579mol) dimethyldimethoxysilane, react for 1h under magnetic stirring at room temperature, add 30g (0.4995mol) Urea, and continue to stir for 0.5h to obtain a clear sol solution;
[0029] b. Gelation of the sol: put the sol solution obtained in step a into a closed beaker system, and gelatinize at a temperature of 90° C. for 3 hours to obtain a silicone sponge;
[0030] c. Cleaning and drying of the siloxane sponge: the siloxane sponge obtained in step b is sequentially soaked and squeezed with methanol, deionized water, and methanol for 0.5h, and then placed at a temperature of 40 °C for 9 hours to obtain a tertiary siloxane sponge.
Embodiment 2
[0032] a. Hydrolysis of alkoxysilane to form a sol: 3.9g (0.0123mol) cetyltrimethylammonium chloride was added to 150mL (8.3333mol) of nitric acid solution with pH = 3.5, and then 3.7g (0.0240mol) was added successively ) tetramethoxysilane, 17g (0.0954mol) methyltriethoxysilane, 46.9g (0.2662mol) diethyldiethoxysilane, reacted for 0.5h under magnetic stirring at room temperature, and added 50ml ( 0.75mol) ethylenediamine and continued to stir for 1h to obtain a clear sol solution;
[0033] b. Gelation of the sol: put the sol solution obtained in step a into a closed beaker system, and gelatinize at a temperature of 70° C. for 9 hours to obtain a silicone sponge;
[0034] c. Cleaning and drying of the siloxane sponge: the siloxane sponge obtained in step b is sequentially soaked and squeezed with ethanol, deionized water, and ethanol for 0.5 hours, and then placed at a temperature of 35 Dry at °C for 12 hours to obtain a tertiary silicone sponge.
Embodiment 3
[0036] a. Hydrolysis of alkoxysilane to form a sol: 8.0g (0.0220mol) of cetyltrimethylammonium bromide was added to 170mL (9.4444mol) of hydrochloric acid solution with pH=5, and then 12.7g (0.0480mol) of ) tetrapropoxysilane, 13.1g (0.0881mol) vinyltrimethoxysilane, 32.9g (0.2745mol) dimethyldimethoxysilane, reacted for 0.5h under magnetic stirring at room temperature, and added 60g ( 0.4110mol) triethylenetetramine and continue to stir 1h, obtain clear sol solution;
[0037] b. Gelation of the sol: put the sol solution obtained in step a into a closed beaker system, and gelatinize at a temperature of 80° C. for 12 hours to obtain a silicone sponge;
[0038] c. Cleaning and drying of the siloxane sponge: the siloxane sponge obtained in step b is sequentially soaked and extruded in isopropanol, deionized water, and isopropanol for 0.5h each soaking and extruding, and then Dry at a temperature of 25°C for 24 hours to obtain a tertiary siloxane sponge.
PUM
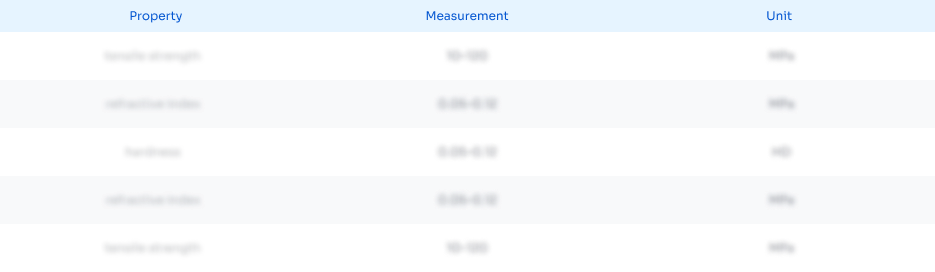
Abstract
Description
Claims
Application Information

- R&D
- Intellectual Property
- Life Sciences
- Materials
- Tech Scout
- Unparalleled Data Quality
- Higher Quality Content
- 60% Fewer Hallucinations
Browse by: Latest US Patents, China's latest patents, Technical Efficacy Thesaurus, Application Domain, Technology Topic, Popular Technical Reports.
© 2025 PatSnap. All rights reserved.Legal|Privacy policy|Modern Slavery Act Transparency Statement|Sitemap|About US| Contact US: help@patsnap.com