Molybdenum-based composite metal oxide catalyst for synthesizing propenyl alcohol by glycerol and preparation method of molybdenum-based composite metal oxide catalyst
A composite metal and oxide technology, applied in the chemical industry, can solve the problems of low selectivity of propenyl alcohol and low economic application value, and achieve the effects of simple preparation process and important economic and social value
- Summary
- Abstract
- Description
- Claims
- Application Information
AI Technical Summary
Problems solved by technology
Method used
Examples
Embodiment 1
[0017] Weigh 8.0 g Mo(NO 3 ) 3 .5H 2 O and 1.0 g Zr(NO 3 ) 2 .5H 2 O is placed in a beaker, add 100 ml of deionized water and stir continuously to promote the complete mixing of solids and salts. 2.0 M (NH 4 ) 2 CO 3 The solution was slowly added dropwise to the mixed solution until the precipitation was complete. After filtration, the filter residue was stirred in 100 ml deionized water at 60 °C for 0.5 h. Then filter and wash to neutral, and ventilate and dry at 80 °C. After drying, the mixture was heated and calcined at 550 °C for 6 h in an air atmosphere in a muffle furnace to obtain Mo 10 Zr 1 o z composite oxide catalyst.
[0018] Will Mo 10 Zr 1 o z The composite oxide catalyst was tabletted and sieved to obtain 1.0 g of 20-40 mesh catalyst particles, which were filled in a constant temperature section of a reaction tube with a diameter of 8 mm, and quartz sand was paved front and back. A metering pump was used to inject 20 wt% glycerol aqueous solution...
Embodiment 2
[0020] Weigh 10.0 g Mo(NO 3 ) 3 .5H 2 O and 1.0 g Ni(NO 3 ) 2 .6H 2 O is placed in a beaker, add 100 ml of deionized water and stir continuously to promote the complete mixing of solids and salts. 1.0 M (NH 4 ) 2 C 2 o 4 The solution was slowly added dropwise to the mixed solution until the precipitation was complete. After filtration, the filter residue was stirred in 100 ml deionized water at 60 °C for 0.5 h. Then filter and wash to neutral, and ventilate and dry at 80 °C. After drying, the mixture was heated and calcined at 550 °C for 6 h in an air atmosphere in a muffle furnace to obtain Mo 8 Ni 1 o z composite oxide catalyst.
[0021] Will Mo 8 Ni 1 o z The composite oxide catalyst was tabletted and sieved to obtain 1.0 g of 20-40 mesh catalyst particles, which were filled in a constant temperature section of a reaction tube with a diameter of 8 mm, and quartz sand was paved front and back. The reactivity evaluation method and product analysis method are...
Embodiment 3
[0023] Weigh 8.0 g Mo(NO 3 ) 3 .5H 2 O and 1.5 g Fe(NO 3 ) 3 .9H 2 O is placed in a beaker, add 100 ml of deionized water and stir continuously to promote the complete mixing of solids and salts. 2.0 M (NH 4 ) 2 CO 3The solution was slowly added dropwise to the mixed solution until the precipitation was complete. After filtration, the filter residue was stirred in 100 ml deionized water at 60 °C for 0.5 h. Then filter and wash to neutral, and ventilate and dry at 80 °C. After drying, the mixture was heated and calcined at 550 °C for 6 h in an air atmosphere in a muffle furnace to obtain Mo 6 Fe 1 o z composite oxide catalyst.
[0024] Will Mo 6 Fe 1 o z The composite oxide catalyst was tabletted and sieved to obtain 1.0 g of 20-40 mesh catalyst particles, which were filled in a constant temperature section of a reaction tube with a diameter of 8 mm, and quartz sand was paved front and back. The catalyst activity evaluation method is as in Example 1. The react...
PUM
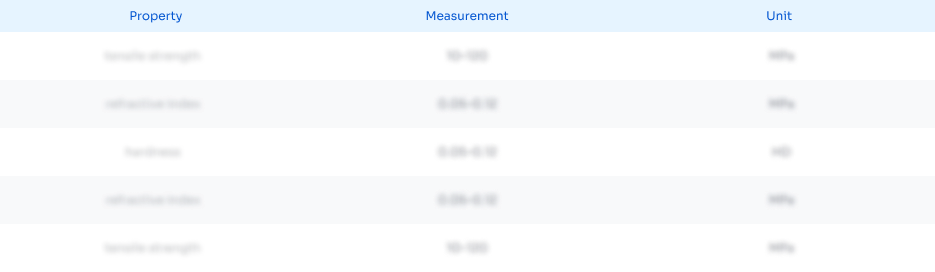
Abstract
Description
Claims
Application Information

- R&D Engineer
- R&D Manager
- IP Professional
- Industry Leading Data Capabilities
- Powerful AI technology
- Patent DNA Extraction
Browse by: Latest US Patents, China's latest patents, Technical Efficacy Thesaurus, Application Domain, Technology Topic, Popular Technical Reports.
© 2024 PatSnap. All rights reserved.Legal|Privacy policy|Modern Slavery Act Transparency Statement|Sitemap|About US| Contact US: help@patsnap.com