Base plate for printed circuit board drilling and preparation method for base plate
A technology for printed circuit boards and backing plates, which is applied in printed circuit manufacturing, printed circuits, drilling/drilling equipment, etc., can solve the problems of insufficient lubrication and heat dissipation capacity of drilling backing plates, and achieve good industrial production value and application prospects. , The effect of improving the quality of the hole wall and increasing the accuracy of the hole position
- Summary
- Abstract
- Description
- Claims
- Application Information
AI Technical Summary
Problems solved by technology
Method used
Image
Examples
Embodiment 1
[0036] In parts by weight, 95 parts of the main component of the lubricating and heat-dissipating resin are mixed with 5 parts of additives to form an emulsion. The main component of the lubricating and heat-dissipating resin is composed of 10 parts of polyethylene oxide, 10 parts of polyethylene glycol, 3 parts of glycerin, and 30 parts of vinyl acetate in parts by weight, and the auxiliary agent is a silicone surfactant. The emulsion is sprayed on the surface of the wood fiber board by a coating machine. Before the emulsion is completely dry, paste the wood pulp paper on the lubricating heat dissipation resin, and then dry it.
[0037] In parts by weight, 100 parts of unsaturated polyester, 2 parts of initiator and 0.4 part of accelerator are taken, wherein the unsaturated polyester is synthesized from maleic anhydride, phthalic anhydride and propylene glycol. The initiator is cyclohexanone peroxide, and the accelerator is cobalt naphthenate. The mixed components are coate...
Embodiment 2
[0039] In parts by weight, 95 parts of the main component of the lubricating and heat-dissipating resin are mixed with 5 parts of additives to form an emulsion. The main component of the lubricating and heat-dissipating resin is composed of 10 parts of polyethylene oxide, 10 parts of polyethylene glycol, 2 parts of glycerin, and 40 parts of polyvinyl alcohol, and the auxiliary agent is silicone surfactant. The emulsion is sprayed on the surface of the wood fiber board by a coating machine. Before the emulsion is completely dry, paste the wood pulp paper on the lubricating heat dissipation resin, and then dry it.
[0040] In parts by weight, get 100 parts of unsaturated polyester, 2 parts of initiator, 0.4 part of accelerator, and 0.5 part of inhibitor, wherein the unsaturated polyester is composed of maleic anhydride, phthalic anhydride and propylene glycol Synthesized. The initiator is cyclohexanone peroxide, the accelerator is cobalt naphthenate, and the inhibitor is hydro...
Embodiment 3
[0042]In parts by weight, 95 parts of the main component of the lubricating and heat-dissipating resin are mixed with 5 parts of additives to form an emulsion. The main component of the lubricating and heat-dissipating resin is composed of 30 parts of polyethylene oxide, 30 parts of polyethylene glycol, 8 parts of glycerin, and 60 parts of vinyl acetate in parts by weight, and the auxiliary agent is a silicone surfactant. The emulsion is sprayed on the surface of the wood fiber board by a coating machine. Before the emulsion is completely dry, paste the wood pulp paper on the lubricating heat dissipation resin, and then dry it.
[0043] In parts by weight, 100 parts of unsaturated polyester, 4 parts of initiator and 2 parts of accelerator are taken, wherein the unsaturated polyester is synthesized from maleic anhydride, phthalic anhydride and propylene glycol. The initiator is cyclohexanone peroxide, and the accelerator is cobalt naphthenate. The mixed components are coated ...
PUM
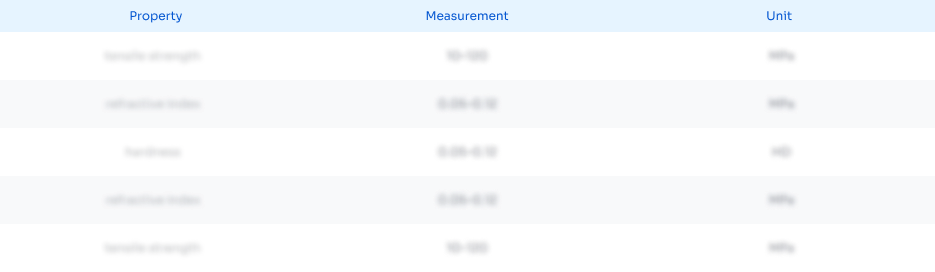
Abstract
Description
Claims
Application Information

- R&D
- Intellectual Property
- Life Sciences
- Materials
- Tech Scout
- Unparalleled Data Quality
- Higher Quality Content
- 60% Fewer Hallucinations
Browse by: Latest US Patents, China's latest patents, Technical Efficacy Thesaurus, Application Domain, Technology Topic, Popular Technical Reports.
© 2025 PatSnap. All rights reserved.Legal|Privacy policy|Modern Slavery Act Transparency Statement|Sitemap|About US| Contact US: help@patsnap.com