Method for controlling high dispersion of metal centers for catalysts by using auxiliaries
A catalyst metal, center height technology, applied in chemical instruments and methods, catalyst activation/preparation, physical/chemical process catalysts, etc., can solve problems such as difficult removal, affecting catalyst activity, and the role of difficult metal active centers
- Summary
- Abstract
- Description
- Claims
- Application Information
AI Technical Summary
Problems solved by technology
Method used
Image
Examples
Embodiment 1
[0021] Step A: 0.01mol Mg(NO 3 ) 2 ·6H 2 O, 0.0015mol Al(NO 3 ) 3 9H 2 O, 0.001mol SnCl 4 ·6H 2 O. 0.2mol urea was dissolved in 200ml deionized water to prepare a mixed solution, crystallized at 90°C for 12h, the product was filtered and washed to pH 7, dried in an oven at 100°C for 10h, and a small amount of samples were taken for characterization to obtain MgAlSn-LDHs.
[0022] Step B: Weigh 2 g of MgAlSn-LDHs (prepared in Step A), impregnate an equal volume of H 2 [PtCl 6 ]·6H 2 O aqueous solution, oscillated evenly, washed to remove physically adsorbed ions, and dried at 80°C for 12 hours to obtain Pt / MgAlSn-LDHs.
[0023] Step C: heat the obtained Pt / MgAlSn-LDHs in a muffle furnace at 750 °C for 300 min, and after cooling down to room temperature, in a tube furnace for H 2 Reduction, reduction at 750°C for 300 minutes to obtain Pt / MgAlSn-MMO, a small amount of samples were taken for characterization.
Embodiment 2
[0029] Step A: 0.01mol Zn(NO 3 ) 2 ·6H 2 O, 0.0015mol Al(NO 3 ) 3 9H 2 O, 0.001mol SnCl 4 ·6H 2 O. 0.2mol urea was dissolved in 200ml deionized water to prepare a mixed solution, crystallized at 90°C for 12h, the product was filtered and washed to pH 7, dried in an oven at 100°C for 10h, and a small amount of samples were taken for characterization to obtain ZnAlSn-LDHs.
[0030] Step B: Weigh 2g ZnAlSn-LDHs (prepared in step A), impregnate an equal volume of H 2 [PtCl 6 ]·6H 2 O aqueous solution, oscillated evenly, washed to remove physically adsorbed ions, and dried at 80°C for 12 hours to obtain Pt / ZnAlSn-LDHs.
[0031] Step C: heat the obtained Pt / ZnAlSn-LDHs in a muffle furnace at 750 °C for 300 min, and after cooling down to room temperature, heat it in a tube furnace for H 2 Reduction, reduction at 750°C for 300 minutes to obtain Pt / ZnAlSn-MMO, a small amount of samples were taken for characterization.
Embodiment 3
[0037] Step A: 0.01mol Zn(NO 3 ) 2 ·6H 2 O, 0.0015mol Al(NO 3 ) 3 9H 2 O, 0.001mol ZrO(NO 3 ) 2 ·6H 2 O. Dissolve 0.2mol urea in 200ml deionized water to prepare a mixed solution, stir and crystallize at 90°C for 12h, filter and wash the product to pH 7, dry in an oven at 100°C for 10h, take a small amount of samples for characterization, and obtain ZnAlZr-LDHs.
[0038] Step B: Weigh 2g of ZnAlZr-LDHs (prepared in step A), impregnate an equal volume of H 2 [PtCl 6 ] aqueous solution, shake evenly, wash to remove physically adsorbed ions, and dry at 100°C for 12 hours to obtain Pt / ZnAlZr-LDHs.
[0039] Step C: heat the obtained Pt / ZnAlZr-LDHs in a muffle furnace at 750 ° C for 300 min, and after cooling down to room temperature, heat 2 Reduction, reduction at 750°C for 300 minutes to obtain Pt / ZnAlZr-MMO, a small amount of samples were taken for characterization.
PUM
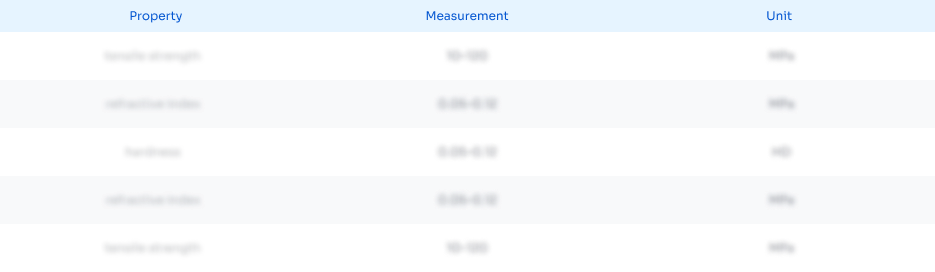
Abstract
Description
Claims
Application Information

- R&D
- Intellectual Property
- Life Sciences
- Materials
- Tech Scout
- Unparalleled Data Quality
- Higher Quality Content
- 60% Fewer Hallucinations
Browse by: Latest US Patents, China's latest patents, Technical Efficacy Thesaurus, Application Domain, Technology Topic, Popular Technical Reports.
© 2025 PatSnap. All rights reserved.Legal|Privacy policy|Modern Slavery Act Transparency Statement|Sitemap|About US| Contact US: help@patsnap.com