Self-enhanced thin-wall miniature balloon and manufacturing method thereof
A technology of balloons and balloon tubes, applied in medical science, internal bone synthesis, internal fixators, etc., to achieve the effect of increasing the number and enhancing the tear resistance
- Summary
- Abstract
- Description
- Claims
- Application Information
AI Technical Summary
Problems solved by technology
Method used
Image
Examples
preparation example Construction
[0048] The preparation method of the present invention comprises the following steps: the thermoplastic elastomer tube blank undergoes multi-stage expansion to obtain a self-reinforced expansion tube; the self-reinforcing expansion tube is molded by a balloon mold to obtain a balloon tube; the balloon tube is coaxially Reverse stretching yields a self-reinforcing balloon.
[0049]Specifically, polyurethane thermoplastic elastomer pipes (also known as pipe blanks) are selected, and the pipes are expanded axially and circumferentially for 2-5 times. Taking two axial and circumferential expansions of the pipe as an example, the method of axial and circumferential expansion is described. The pipe material 10 is optionally heated to a high elastic state, and the pipe material 10 is pulled, and the pulling speed at both ends is different, and the pulling speed difference axially stretches the tube blank 10 to perform axial expansion, such as figure 2 As shown, at the same time, th...
Embodiment 1
[0057] Cut 100mm of thermoplastic polyurethane original pipe of φ3.2mm×0.6mm. Heat a copper primary conical expansion rod with a cone angle of 30°, a cone length of 20mm, an outer diameter of 5mm, and a length of 200mm to 100°C. Pull both ends of the original pipe, the front pulling speed is 4m / min, the rear pulling speed is 3m / min, the original pipe to be expanded is drawn into the rotating primary expansion rod and the original pipe is expanded, and the expansion rod and the original Put the tubes together into a 5°C water bath for cooling, and withdraw the first-stage expansion rod to obtain the first-stage expansion tube.
[0058] Heat a copper secondary conical expansion rod with a cone angle of 45°, a cone length of 20mm, an outer diameter of 8mm, and a length of 200mm to 100°C. Pull the two ends of the first-stage expansion tube, the front traction speed is 3m / min, and the rear traction speed is 2.2m / min, pull the first-stage expansion tube into the rotating second-lev...
Embodiment 2
[0063] Cut 150mm of thermoplastic polyurethane original pipe of φ3.0mm×0.5mm. Heat a copper primary conical expansion rod with a cone angle of 40°, a cone length of 20mm, an outer diameter of 4mm, and a length of 200mm to 100°C. Pull the two ends of the original pipe, the front traction speed is 4.6m / min, the rear traction speed is 3.5m / min, the original pipe to be expanded is drawn into the rotating primary expansion rod and the original pipe is expanded, and the expansion rod Put it into a 20°C water bath to cool down together with the original tube, withdraw the first-level expansion rod, and obtain the first-level expansion tube.
[0064] Heat a copper secondary conical expansion rod with a cone angle of 55°, a cone length of 20mm, an outer diameter of 6mm, and a length of 200mm to 110°C. Pull the two ends of the first-stage expansion tube, the front traction speed is 3m / min, the rear traction speed is 1.6m / min, pull the first-stage expansion tube into the rotating second...
PUM
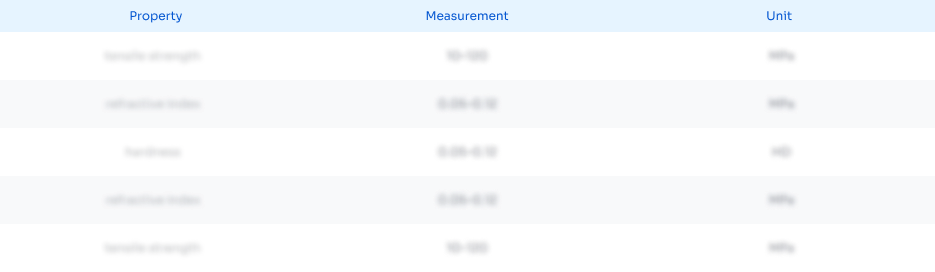
Abstract
Description
Claims
Application Information

- Generate Ideas
- Intellectual Property
- Life Sciences
- Materials
- Tech Scout
- Unparalleled Data Quality
- Higher Quality Content
- 60% Fewer Hallucinations
Browse by: Latest US Patents, China's latest patents, Technical Efficacy Thesaurus, Application Domain, Technology Topic, Popular Technical Reports.
© 2025 PatSnap. All rights reserved.Legal|Privacy policy|Modern Slavery Act Transparency Statement|Sitemap|About US| Contact US: help@patsnap.com