Heat-resisting and wear-resisting iron-based self-lubricating material
A self-lubricating material and heat-resistant technology, applied in the field of wear-resistant materials, can solve the problems of low operating temperature, high hardness, and high cost, and achieve the effects of excellent friction performance, low friction coefficient, and good thermal strength
- Summary
- Abstract
- Description
- Claims
- Application Information
AI Technical Summary
Problems solved by technology
Method used
Examples
Embodiment 1
[0012] Weigh 100 meshes of reduced iron powder, 200 meshes of electrolytic copper powder, 200 meshes of ball milled chromium powder, 200 meshes of electrolytic manganese powder, 200 meshes of reduced molybdenum powder, and 4 microns of reduced cobalt powder; analyze pure graphite powder; colloidal molybdenum disulfide powder and Other heat-resistant lubricants and ultra-fine wear-resistant alloy powders. The above powder, according to its degree of oxidation, needs to be reduced if necessary, and then mixed. When mixing, first dry mix various powders other than graphite powder for 6 hours, then add graphite powder and wet mix with alcohol, and mix after vacuum drying. The material process is completed. Putting the mixed powder into the composite mold for electric spark sintering can obtain the heat-resistant and wear-resistant iron-based self-lubricating material. Electric spark sintering can endow the material with full density and ensure the density uniformity of larger-siz...
Embodiment 2
[0015] Weigh 200 meshes of reduced iron powder, 400 meshes of electrolytic copper powder, 400 meshes of ball milled chromium powder, 400 meshes of electrolytic manganese powder, 400 meshes of reduced molybdenum powder, and 8 microns of reduced cobalt powder; analyze pure graphite powder; colloidal molybdenum disulfide powder and Other heat-resistant lubricants and ultra-fine wear-resistant alloy powders. The above powder, according to its degree of oxidation, needs to be reduced if necessary, and then mixed. When mixing, first dry mix various powders other than graphite powder for 10 hours, then add graphite powder and wet mix with alcohol, and mix after vacuum drying. The material process is completed. Putting the mixed powder into the composite mold for electric spark sintering can obtain the heat-resistant and wear-resistant iron-based self-lubricating material. Electric spark sintering can endow the material with full density and ensure the density uniformity of larger-si...
Embodiment 3
[0018] Weigh 150 meshes of reduced iron powder, 300 meshes of electrolytic copper powder, 300 meshes of ball milled chromium powder, 300 meshes of electrolytic manganese powder, 300 meshes of reduced molybdenum powder, and 6 micron order of reduced cobalt powder; analyze pure graphite powder; colloidal molybdenum disulfide powder and Other heat-resistant lubricants and ultra-fine wear-resistant alloy powders. The above powder, according to its degree of oxidation, needs to be reduced if necessary, and then mixed. When mixing, dry mix various powders other than graphite powder for 8 hours, then add graphite powder and wet mix with alcohol, and mix after vacuum drying. The material process is completed. Putting the mixed powder into the composite mold for electric spark sintering can obtain the heat-resistant and wear-resistant iron-based self-lubricating material. Electric spark sintering can endow the material with full density and ensure the density uniformity of larger-size...
PUM
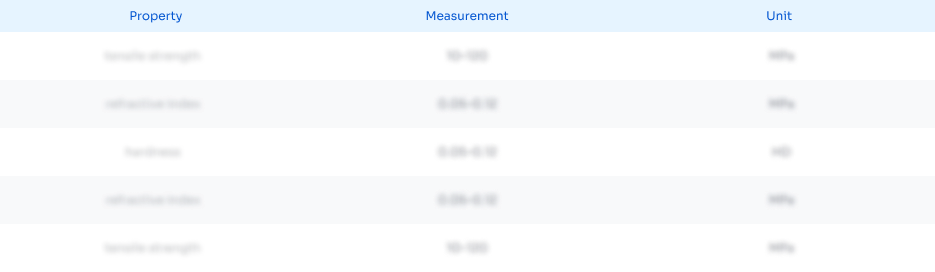
Abstract
Description
Claims
Application Information

- R&D Engineer
- R&D Manager
- IP Professional
- Industry Leading Data Capabilities
- Powerful AI technology
- Patent DNA Extraction
Browse by: Latest US Patents, China's latest patents, Technical Efficacy Thesaurus, Application Domain, Technology Topic, Popular Technical Reports.
© 2024 PatSnap. All rights reserved.Legal|Privacy policy|Modern Slavery Act Transparency Statement|Sitemap|About US| Contact US: help@patsnap.com