Microwave heating melt electrostatic spinning device
A melt electrospinning and electrospinning technology, applied in textiles and papermaking, filament/thread forming, filament raw material melting, etc., can solve the problem of difficult control of heating temperature and spinning process, complex structure, and difficulty in scale problems such as automated production, to achieve the effects of overcoming the difficulty of temperature control, good safety, and low cost
- Summary
- Abstract
- Description
- Claims
- Application Information
AI Technical Summary
Problems solved by technology
Method used
Image
Examples
Embodiment 1
[0013] Example 1: Preparation of Polyvinylidene Fluoride (PVDF) Nanofibers by Microwave Heating Melt Electrospinning Device
[0014] In this embodiment, PVDF powder is firstly added to the barrel 2, and the propelling pump knob 6 is adjusted to set the parameters of the propelling pump 1, the feeding propelling rate is controlled, the specific flow propelling rate is displayed on the electronic display screen 15, and then the propelling pump is turned on. Switch 7, under the propulsion action of the propulsion pump, push the PVDF raw material into the material pipe 5; adjust the microwave frequency adjustment knob 8 in the microwave heating chamber 3, and select the microwave frequency of 2.4-2.5GHz according to the spinning raw material PVDF for heating, The heating time is set by the temperature knob 9 to 30 seconds to 2 minutes, and the temperature is selected and controlled by the temperature control knob 10. The set temperature is 205-235°C, which is 175°C higher than the ...
Embodiment 2
[0015] Example 2: Preparation of polyvinylidene fluoride / polyurethane (PVDF / PU) composite nanofibers by microwave heating melt electrospinning device
[0016] In this example, PVDF and PU powder with a mass ratio of 80:20 are mixed uniformly, and then added to the barrel 2, and the flow knob 6 of the propelling pump is adjusted to set the parameters of the propelling pump 1, and the feeding propulsion rate is controlled. The display screen 15 displays the specific flow rate of advance, turn on the push pump switch 7, and push the PVDF / PU raw material into the material pipe 5 under the propulsion action of the push pump; in the microwave heating chamber 3, adjust the microwave frequency adjustment knob 8, According to the spinning raw material PVDF / PU, the microwave frequency is selected to be 2.4~2.5GHz for heating. The heating time is set by the temperature knob 9 to 30 seconds to 2 minutes, and the temperature is selected and controlled by the temperature control knob 10, and...
PUM
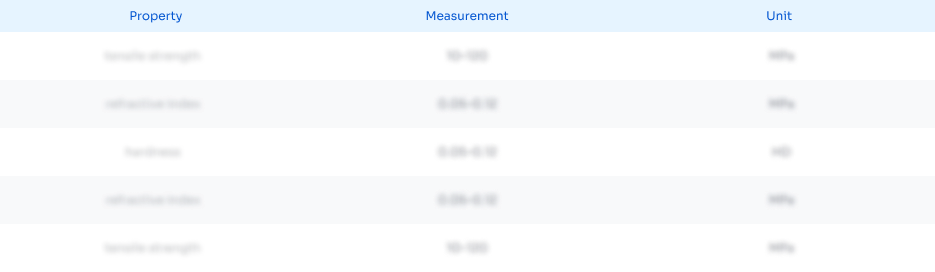
Abstract
Description
Claims
Application Information

- R&D
- Intellectual Property
- Life Sciences
- Materials
- Tech Scout
- Unparalleled Data Quality
- Higher Quality Content
- 60% Fewer Hallucinations
Browse by: Latest US Patents, China's latest patents, Technical Efficacy Thesaurus, Application Domain, Technology Topic, Popular Technical Reports.
© 2025 PatSnap. All rights reserved.Legal|Privacy policy|Modern Slavery Act Transparency Statement|Sitemap|About US| Contact US: help@patsnap.com