Method for manufacturing immiscible alloy ingot casting in aluminothermic reduction-slag refining mode
An immiscible alloy and slag refining technology, which is applied in the field of metallurgy, can solve the problems of high inclusions in alloy ingots, large fluctuations in alloy composition, and many pore defects, and achieve oxygen content removal, raw material cost reduction, and simple operation Effect
- Summary
- Abstract
- Description
- Claims
- Application Information
AI Technical Summary
Problems solved by technology
Method used
Examples
Embodiment 1
[0061] According to the composition of the immiscible alloy ingot to be prepared, three parts of metal oxide powder are respectively prepared, and the metal oxide powder is Cu-based metal oxide powder, which is composed of CuO powder and PbO powder;
[0062] Mix each part of metal oxide powder with Al powder respectively, then add slag-forming agent CaO, respectively, in each part, CaO accounts for 2%, 3% and 5% of the total weight of metal oxide powder and Al powder, and mix all the materials. After uniformity, three batches of materials to be reduced are made;
[0063] The mixing ratios of CuO powder, PbO powder and Al powder are respectively 100:4.5:28, 100:320:60 and 100:775:105 by weight when each part is mixed and batched;
[0064] Put the materials to be reduced into the reactor respectively, and put Mg powder on the surface of the materials to be reduced, ignite the Mg powder directly with an open flame, and initiate the aluminothermic reduction reaction. Three high-t...
Embodiment 2
[0072] According to the composition of the immiscible alloy ingot to be prepared, three parts of immiscible metal oxide powder are respectively prepared, and the metal oxide powder is Cu-based metal oxide powder, which is composed of CuO powder and CoO powder;
[0073] Mix each part of metal oxide powder with Al powder respectively, then add slag-forming agent CaO, respectively, in each part, CaO accounts for 2%, 3% and 5% of the total weight of metal oxide powder and Al powder, and mix all the materials. After uniformity, three batches of materials to be reduced are made;
[0074] The mixing ratios of CuO powder, CoO powder and Al powder are respectively 100:6:30, 100:150:90 and 100:350:175 by weight when each part is mixed and batched;
[0075] Put the materials to be reduced into the reactor respectively, and put Mg powder on the surface of the materials to be reduced, ignite the Mg powder directly with an open flame, and initiate the aluminothermic reduction reaction. Thr...
Embodiment 3
[0083] According to the composition of the immiscible alloy ingot to be prepared, three parts of metal oxide powder are prepared respectively. The metal oxide powder is Cu-based metal oxide powder, which is composed of CuO powder and Fe 2 O 3 powder composition;
[0084] Mix each part of metal oxide powder with Al powder respectively, then add slag-forming agent CaO, respectively, in each part, CaO accounts for 2%, 3% and 5% of the total weight of metal oxide powder and Al powder, and mix all the materials. After uniformity, three batches of materials to be reduced are made;
[0085]CuO powder, Fe 2 O 3 The mixing ratios of powder and Al powder are respectively 100:5.5:30, 100:50:48 and 100:115:75 by weight;
[0086] Put the materials to be reduced into the reactor respectively, and put Mg powder on the surface of the materials to be reduced, ignite the Mg powder directly with an open flame, and initiate the aluminothermic reduction reaction. Three high-temperature melts ...
PUM
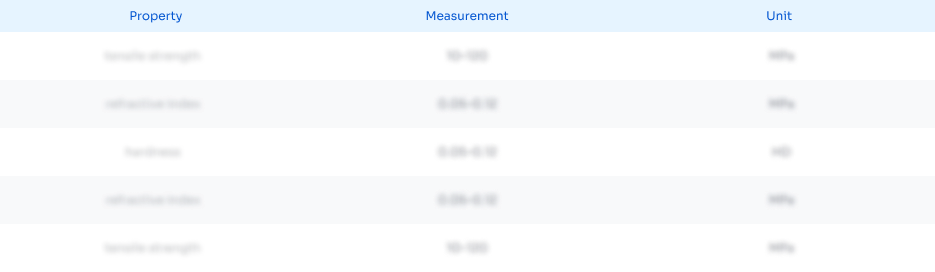
Abstract
Description
Claims
Application Information

- Generate Ideas
- Intellectual Property
- Life Sciences
- Materials
- Tech Scout
- Unparalleled Data Quality
- Higher Quality Content
- 60% Fewer Hallucinations
Browse by: Latest US Patents, China's latest patents, Technical Efficacy Thesaurus, Application Domain, Technology Topic, Popular Technical Reports.
© 2025 PatSnap. All rights reserved.Legal|Privacy policy|Modern Slavery Act Transparency Statement|Sitemap|About US| Contact US: help@patsnap.com