Environment-friendly, energy-saving and carbon-reducing TPU molding method and device thereof
An environment-friendly, energy-saving, molding device technology, applied in coating and other directions, can solve the problems of inconvenient material preparation, increased production costs, and huge energy for users, and achieves the effect of omitting energy consumption
- Summary
- Abstract
- Description
- Claims
- Application Information
AI Technical Summary
Problems solved by technology
Method used
Image
Examples
Embodiment Construction
[0044] In order to further understand the features and technical contents of the present invention, please refer to the following detailed description and accompanying drawings of the present invention, which are only provided for reference and description, and are not intended to limit the present invention.
[0045] see figure 1 As shown, it is a flow chart of the steps of the first preferred embodiment of the present invention, which discloses a molding method of an environmentally friendly, energy-saving and carbon-reducing TPU (thermoplastic polyurethane elastomer rubber), and the molding method of the environmentally-friendly, energy-saving and carbon-reducing TPU includes Follow these steps:
[0046] Material preparation step: prepare an isocyanate polymer containing NCO (isocyanate group), a hydroxyl compound containing OH (hydroxyl group) and a chain extender.
[0047] A mixing step: mixing the isocyanate polymer containing NCO (isocyanate group), the hydroxyl compou...
PUM
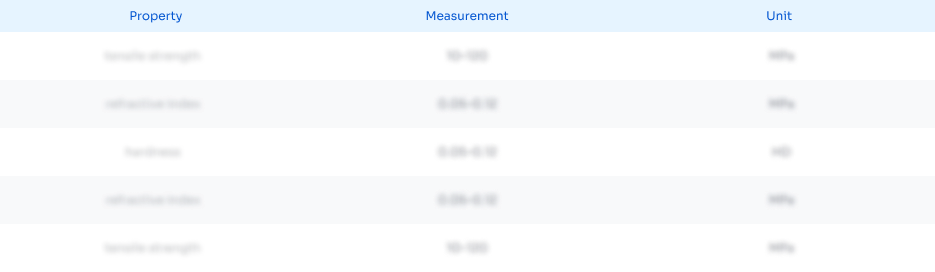
Abstract
Description
Claims
Application Information

- Generate Ideas
- Intellectual Property
- Life Sciences
- Materials
- Tech Scout
- Unparalleled Data Quality
- Higher Quality Content
- 60% Fewer Hallucinations
Browse by: Latest US Patents, China's latest patents, Technical Efficacy Thesaurus, Application Domain, Technology Topic, Popular Technical Reports.
© 2025 PatSnap. All rights reserved.Legal|Privacy policy|Modern Slavery Act Transparency Statement|Sitemap|About US| Contact US: help@patsnap.com