Backward GPP (Glass Passivation Pellet) high voltage diode chip in automobile module, and production technology
A high-voltage diode and production process technology, which is applied in the field of reverse GPP high-voltage diode chip and production process, can solve the problems of reverse diode glass passivation protection damage, large diode leakage current, and reduced welding area to achieve enhanced stability And anti-surge ability, reduce leakage, reduce the effect of body pressure drop
- Summary
- Abstract
- Description
- Claims
- Application Information
AI Technical Summary
Problems solved by technology
Method used
Image
Examples
Embodiment Construction
[0035] In order to make the technical means, creative features, goals and effects achieved by the present invention easy to understand, the present invention will be further described below in conjunction with specific illustrations.
[0036] A kind of production technology of reverse GPP high-voltage diode chip in automobile module, see image 3 , which has the following steps:
[0037] (1) Pre-oxidation treatment: chemically treat the surface of silicon wafers through electronic cleaning agents, deionized water cleaning and other processes to obtain clean original silicon wafers.
[0038] (2) Oxidation: Put the cleaned original silicon wafer in an oxidation furnace at 1100-1200°C to grow a layer of oxide layer as a mask to prevent the boron diffusion source from entering the N + Surface, open grooves.
[0039] (3) Photolithography: Apply glue, expose, and develop the oxidized silicon wafer to form a mesa pattern.
[0040] (4) Removal of the single-side oxide layer: remove...
PUM
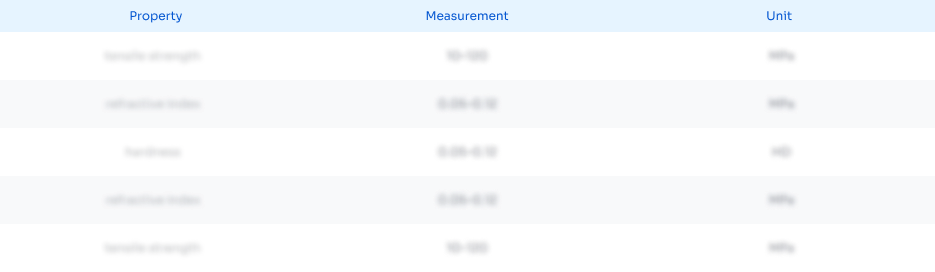
Abstract
Description
Claims
Application Information

- R&D
- Intellectual Property
- Life Sciences
- Materials
- Tech Scout
- Unparalleled Data Quality
- Higher Quality Content
- 60% Fewer Hallucinations
Browse by: Latest US Patents, China's latest patents, Technical Efficacy Thesaurus, Application Domain, Technology Topic, Popular Technical Reports.
© 2025 PatSnap. All rights reserved.Legal|Privacy policy|Modern Slavery Act Transparency Statement|Sitemap|About US| Contact US: help@patsnap.com