Offset heat transfer printed logo, forming process and forming device
A molding process and thermal transfer printing technology, which is applied to rotary printing machines, printing, sealing, etc., can solve the problems of limited service range of printing factories, high handling and transportation costs, and damage to clothing, etc., to achieve light weight, small size, The effect of low transportation costs
- Summary
- Abstract
- Description
- Claims
- Application Information
AI Technical Summary
Problems solved by technology
Method used
Image
Examples
Embodiment Construction
[0036] In order to further explain the technical solution of the present invention, the present invention will be described in detail below through specific examples.
[0037] Such as figure 1 As shown, it is an offset thermal transfer trademark logo related to the present invention, including a PET film 11, a release layer 12, a pattern layer 13, a white ink layer 14, a bullet-through layer 15 and a hot-melt adhesive layer 16. The pattern layer 12 , the pattern layer 13 , the white ink layer 14 , the bullet-through layer 15 and the hot-melt adhesive layer 16 are sequentially formed on the PET film 11 . Preferably, the white ink layer 14 has three layers stacked one after the other and independent of each other. Specifically, the white ink layer 14 is printed three times by a screen printing machine during forming, and undergoes a drying operation after each printing. Likewise, the hot melt adhesive layer 16 has three layers stacked in sequence and independent of each other. ...
PUM
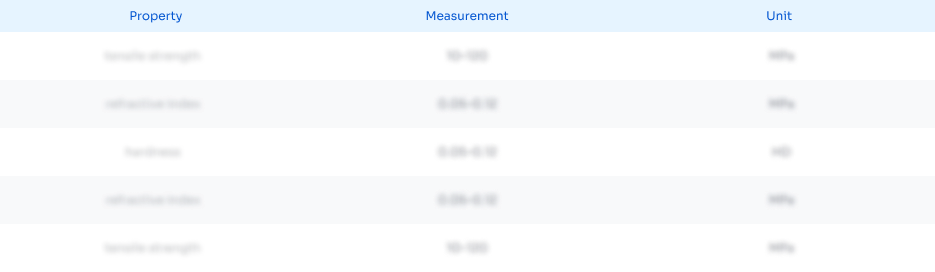
Abstract
Description
Claims
Application Information

- R&D
- Intellectual Property
- Life Sciences
- Materials
- Tech Scout
- Unparalleled Data Quality
- Higher Quality Content
- 60% Fewer Hallucinations
Browse by: Latest US Patents, China's latest patents, Technical Efficacy Thesaurus, Application Domain, Technology Topic, Popular Technical Reports.
© 2025 PatSnap. All rights reserved.Legal|Privacy policy|Modern Slavery Act Transparency Statement|Sitemap|About US| Contact US: help@patsnap.com