Crack-resistant concrete water-reducing and waterproof compacting agent and production method thereof
A technology for waterproofing and compacting concrete, which is applied in the field of anti-cracking concrete water-reducing and waterproofing compacting agent, which can solve the problems of poor anti-cracking effect, high cost, and complicated raw materials, and achieve the effect of high cost performance, low cost and good effect
- Summary
- Abstract
- Description
- Claims
- Application Information
AI Technical Summary
Problems solved by technology
Method used
Image
Examples
Embodiment 1
[0021] (1) Raw material and weight:
[0022] 45 parts by weight of high-performance polycarboxylate superplasticizer with a polyester solid content of 40%; parts by weight of ferric chloride; 5 parts by weight of sodium gluconate; 3 parts by weight of sucrose; 15 parts by weight of water; parts; the air-entraining agent sodium abietate is 0.5 parts by weight.
[0023] (2) Production
[0024] Put ferric chloride into water first, dissolve it completely in water while stirring, let it cool naturally, add sodium gluconate and sucrose, then add high-performance polycarboxylate water reducer, and finally add air-entraining agent and defoamer. According to the above sequence, the raw materials are measured and put into the container, mixed and stirred until they are completely dissolved, then put into the finished product packaging tank, inspected and packaged, and the product is obtained.
Embodiment 2
[0026] (1) Raw material and weight:
[0027] 48 parts by weight of high-performance polycarboxylate superplasticizer with a polyester solid content of 40%; 18 parts by weight of ferric chloride; 10 parts by weight of sodium gluconate; 2 parts by weight of sucrose; 13 parts by weight of water; parts by weight; the air-entraining agent sodium rosinate is 2 parts by weight.
[0028] (2) Production
[0029] First put ferric chloride into water, under stirring, completely dissolve it in water, let it cool naturally, add sodium gluconate and sucrose, then add high-performance polycarboxylate water reducer, and finally add defoamer and air-entraining agents. According to the above sequence, the raw materials are measured and put into the container, mixed and stirred until they are completely dissolved, then put into the finished product packaging tank, inspected and packaged, and the product is obtained.
Embodiment 3
[0031] (1) Raw material and weight:
[0032] 47 parts by weight of high-performance polycarboxylate superplasticizer with polyether type solid content of 40%; 14 parts by weight of ferric chloride, 11 parts by weight of sodium gluconate; 6 parts by weight of sucrose; 15 parts by weight of water; parts by weight; air-entraining agent sodium rosinate is 0.5 parts by weight.
[0033] (2) Production
[0034]Put the ferric chloride into the water firstly, and dissolve it completely in the water while stirring, let it cool down naturally, add sodium gluconate and sucrose, then add high-performance polycarboxylate water reducer, and finally add air-entraining agent and defoamers. According to the above sequence, the raw materials are measured and put into the container, mixed and stirred until they are completely dissolved, then put into the finished product packaging tank, inspected and packaged, and the product is obtained.
PUM
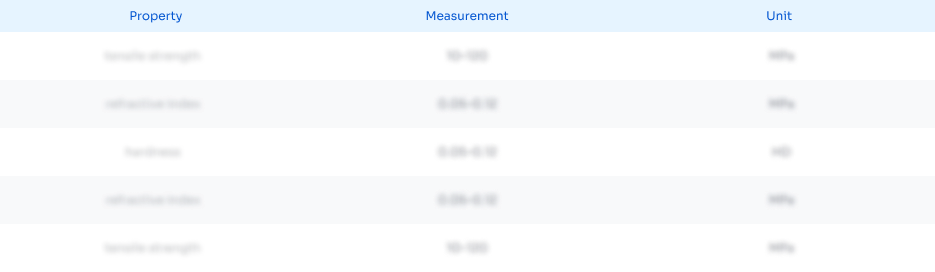
Abstract
Description
Claims
Application Information

- Generate Ideas
- Intellectual Property
- Life Sciences
- Materials
- Tech Scout
- Unparalleled Data Quality
- Higher Quality Content
- 60% Fewer Hallucinations
Browse by: Latest US Patents, China's latest patents, Technical Efficacy Thesaurus, Application Domain, Technology Topic, Popular Technical Reports.
© 2025 PatSnap. All rights reserved.Legal|Privacy policy|Modern Slavery Act Transparency Statement|Sitemap|About US| Contact US: help@patsnap.com