Thermal-mechanical coupling predication method for thickness of white layer on surface of hard tuned workpiece
A prediction method and workpiece surface technology, applied in special data processing applications, instruments, electrical digital data processing, etc., can solve the problem of inability to realize thermal-mechanical coupling, inability to realize high-precision prediction of white layer thickness, and inability to reflect the intrinsic nature of white layer Formation mechanism and other issues
- Summary
- Abstract
- Description
- Claims
- Application Information
AI Technical Summary
Problems solved by technology
Method used
Image
Examples
Embodiment Construction
[0055] The invention takes GCr15 hardened steel as an example to establish a thermomechanical coupling prediction method for the thickness of the surface white layer. The specific implementation steps and embodiments of the present invention will be described in detail below in conjunction with the technical scheme of the present invention and the accompanying drawings.
[0056] Step 1: Carry out finite element modeling and simulation on the GCr15 hard cutting process.
[0057] ①Establish the finite element model of the cutting process: select the meshing method, the constitutive model of the material, the friction model and the boundary conditions, in which the adaptive meshing technology is used for the meshing, and the Johnson-Cook (JC) model is selected for the constitutive model , the Johnson-Cook equation is shown in equation (13):
[0058] σ ‾ = [ A + Bϵ n ...
PUM
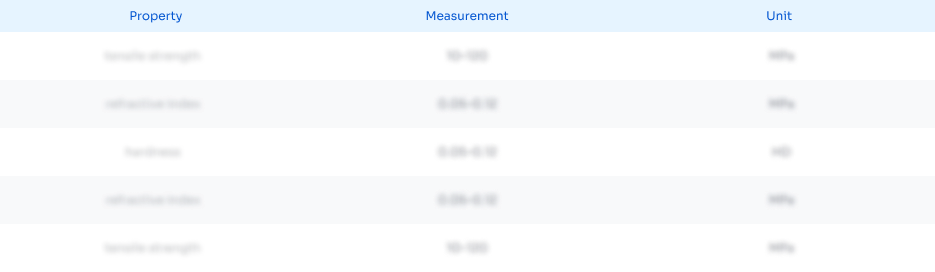
Abstract
Description
Claims
Application Information

- R&D
- Intellectual Property
- Life Sciences
- Materials
- Tech Scout
- Unparalleled Data Quality
- Higher Quality Content
- 60% Fewer Hallucinations
Browse by: Latest US Patents, China's latest patents, Technical Efficacy Thesaurus, Application Domain, Technology Topic, Popular Technical Reports.
© 2025 PatSnap. All rights reserved.Legal|Privacy policy|Modern Slavery Act Transparency Statement|Sitemap|About US| Contact US: help@patsnap.com