A Method for Calculating Theoretical Thickness of Layup Based on Automatic Laying Technology
An automatic wire laying and layering technology, which is applied in the field of laying theoretical thickness calculation based on automatic wire laying technology, can solve the problems of repeated trial and error, large errors, etc., achieve accurate thickness, improve programming efficiency, and avoid actual laying Verify the effect
- Summary
- Abstract
- Description
- Claims
- Application Information
AI Technical Summary
Problems solved by technology
Method used
Image
Examples
Embodiment 1
[0030] A method for calculating the theoretical thickness of a layup based on automatic wire laying technology, comprising the following steps:
[0031] Step S1: Extract the mold-applied surface of the part to be molded, and represent the mold-applied surface with a point cloud, such as figure 1 , get points P1, P2, P3...Pn;
[0032] Step S2: According to the theoretical trajectory of the laying procedure, extract the center lines L1S1, L1S2, L1S3...L1Sn of each tow on the first layup layer L1, and sequentially extract all the lines on the subsequent layup layers L2, L3, L4...Ln center line;
[0033] Step S3: For any layer Ln, find the vertical line between any point Pn of the point cloud and any center line LnSn on the layer, and the length of the vertical line
[0034] Step S4: as figure 2 , according to the calculated distance between the Pn point and the center line, determine whether the Pn point falls in the prepreg coverage area, and then judge each point of the p...
Embodiment 2
[0038] A method for calculating the theoretical thickness of a layup based on automatic wire laying technology, comprising the following steps:
[0039] Step S1: Extract the mold-applied surface of the part to be molded, and represent the mold-applied surface with a point cloud, such as figure 1 , obtain points P1, P2, P3...Pn; when using point cloud to express the die surface, by performing mathematical calculation on each point, the layer thickness information is obtained after screening, wherein the distance between two adjacent points is not greater than the specified value; the specified value is determined according to the width of the automatic wire laying material and the gap between the belts;
[0040] Step S2: According to the theoretical trajectory of the laying procedure, extract the center lines L1S1, L1S2, L1S3...L1Sn of each tow on the first layup layer L1, and sequentially extract all the lines on the subsequent layup layers L2, L3, L4...Ln center line;
[00...
PUM
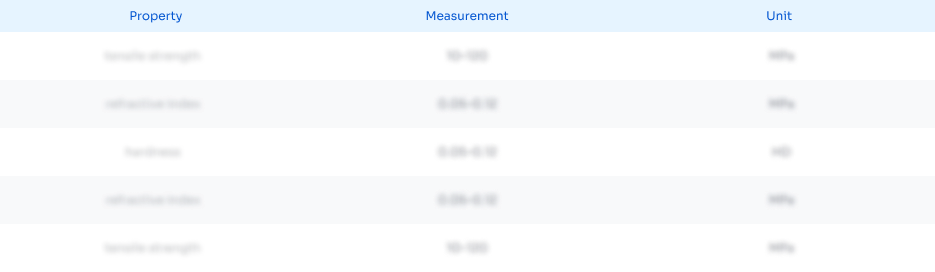
Abstract
Description
Claims
Application Information

- R&D
- Intellectual Property
- Life Sciences
- Materials
- Tech Scout
- Unparalleled Data Quality
- Higher Quality Content
- 60% Fewer Hallucinations
Browse by: Latest US Patents, China's latest patents, Technical Efficacy Thesaurus, Application Domain, Technology Topic, Popular Technical Reports.
© 2025 PatSnap. All rights reserved.Legal|Privacy policy|Modern Slavery Act Transparency Statement|Sitemap|About US| Contact US: help@patsnap.com