Method for preparing modified graphene oxide anti-wear agent
A technology of oxide stone and anti-wear agent, used in additives, petroleum industry, lubricating compositions, etc., can solve the problems of high addition amount, poor mixing uniformity, low utilization rate, etc. Effect
- Summary
- Abstract
- Description
- Claims
- Application Information
AI Technical Summary
Problems solved by technology
Method used
Image
Examples
Embodiment 1
[0019] Add 1.2g of graphene oxide and 3.6g of boric acid into a 250mL three-necked flask, then add 30ml of petroleum ether, stir and add 0.024g of concentrated sulfuric acid, heat up to 60°C for reflux for 8h, and then distill off the solvent. The product was dried in a vacuum oven at 80°C to obtain an off-white solid, which was boric acid-modified graphene oxide. Adding it to ordinary lubricating grease at a ratio of 0.05%, the wear spot diameter is reduced from 0.96 of the blank grease to 0.38, the wear rate is reduced by 60%, the friction coefficient is reduced from 0.106 of the blank grease to 0.04, and the friction coefficient is reduced by 60%.
[0020] Graphene oxide is prepared by the Hummers method, which belongs to the prior art, so the specific preparation method is omitted.
Embodiment 2
[0022] Add 1g of graphene oxide and 0.5g of calcium borate into a 250mL three-neck flask, then add 70ml of n-hexane, stir and heat to 60°C, add 0.005g of concentrated sulfuric acid dropwise, continue to heat up to 150°C, condense and reflux for 2h, and then distill off the solvent. The product was dried in a vacuum oven at 20°C to obtain an off-white solid, which was calcium borate-modified graphene oxide. Adding 0.5% to ordinary grease, the wear spot diameter is reduced from 0.96 of blank grease to 0.20, the wear rate is reduced by 80%, the friction coefficient is reduced from 0.106 of blank grease to 0.02, and the friction coefficient is reduced by 80%.
Embodiment 3
[0024] Add 1g of graphene oxide and 1.5g of lanthanum borate into a 250mL three-neck flask, then add 50ml of ethanol, stir and heat to 80°C, add 0.020g of concentrated sulfuric acid, continue to heat up to 130°C, condense and reflux for 5h, and then distill off the solvent. The product was dried in a vacuum oven at 60°C to obtain an off-white solid which was lanthanum borate graphene oxide. Adding it to ordinary lubricating grease at a ratio of 0.1%, the wear scar diameter is reduced from 0.96 of the blank grease to 0.28, the wear rate is reduced by about 70%, the friction coefficient is reduced from 0.106 of the blank grease to 0.04, and the friction coefficient is reduced by about 60%.
PUM
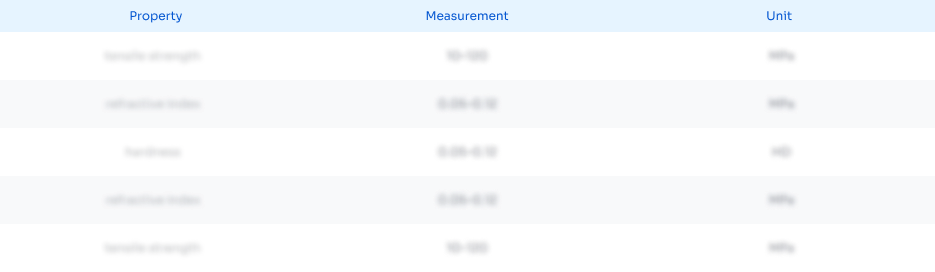
Abstract
Description
Claims
Application Information

- R&D
- Intellectual Property
- Life Sciences
- Materials
- Tech Scout
- Unparalleled Data Quality
- Higher Quality Content
- 60% Fewer Hallucinations
Browse by: Latest US Patents, China's latest patents, Technical Efficacy Thesaurus, Application Domain, Technology Topic, Popular Technical Reports.
© 2025 PatSnap. All rights reserved.Legal|Privacy policy|Modern Slavery Act Transparency Statement|Sitemap|About US| Contact US: help@patsnap.com