Backflow line extrusion forming cutter and backflow line cold extrusion forming process
A molding process, extrusion molding technology, applied in the direction of metal material coating process, etc., can solve the problems of affecting the oil sealing performance of the oil seal, the inability to cut the grain polishing, and affecting the production quality of the oil seal, so as to improve the service life, improve the lubricating performance, The effect of improving oil sealing performance
- Summary
- Abstract
- Description
- Claims
- Application Information
AI Technical Summary
Problems solved by technology
Method used
Image
Examples
Embodiment 1
[0039] The present invention provides the following technical solutions: a reflow line extrusion molding tool and a reflow line cold extrusion molding process, including the following steps:
[0040] S1. Select material;
[0041] S2, annealing treatment;
[0042] S3, machining;
[0043] S4, phosphating and saponification treatment;
[0044] S5, cleaning;
[0045] S6, extrusion molding;
[0046] S7, tempering treatment;
[0047] The S1 process is: select the appropriate alloy material and inspect the material at the same time, so that the surface of the material has no cracks and no stains.
[0048] According to a reflow line extrusion molding tool and reflow line cold extrusion molding process according to the claims, the S2 process is: preheating the selected material, and putting the material into a vacuum intermediate frequency heating furnace for annealing after preheating;
[0049] The preheating temperature is controlled at 42°C for 17 minutes;
[0050] The temper...
Embodiment 2
[0062] The present invention provides the following technical solutions: a reflow line extrusion molding tool and a reflow line cold extrusion molding process, including the following steps:
[0063] S1. Select material;
[0064] S2, annealing treatment;
[0065] S3, machining;
[0066] S4, phosphating and saponification treatment;
[0067] S5, cleaning;
[0068] S6, extrusion molding;
[0069] S7, tempering treatment;
[0070] The S1 process is: select the appropriate alloy material and inspect the material at the same time, so that the surface of the material has no cracks and no stains.
[0071]According to a reflow line extrusion molding tool and reflow line cold extrusion molding process according to the claims, the S2 process is: preheating the selected material, and putting the material into a vacuum intermediate frequency heating furnace for annealing after preheating;
[0072] The preheating temperature is controlled at 45°C for 15 minutes;
[0073] The tempera...
Embodiment 3
[0085] The present invention provides the following technical solutions: a reflow line extrusion molding tool and a reflow line cold extrusion molding process, including the following steps:
[0086] S1. Select material;
[0087] S2, annealing treatment;
[0088] S3, machining;
[0089] S4, phosphating and saponification treatment;
[0090] S5, cleaning;
[0091] S6, extrusion molding;
[0092] S7, tempering treatment;
[0093] The S1 process is: select the appropriate alloy material and inspect the material at the same time, so that the surface of the material has no cracks and no stains.
[0094] According to a reflow line extrusion molding tool and reflow line cold extrusion molding process according to the claims, the S2 process is: preheating the selected material, and putting the material into a vacuum intermediate frequency heating furnace for annealing after preheating;
[0095] The preheating temperature is controlled at 38°C for 19 minutes;
[0096] The temper...
PUM
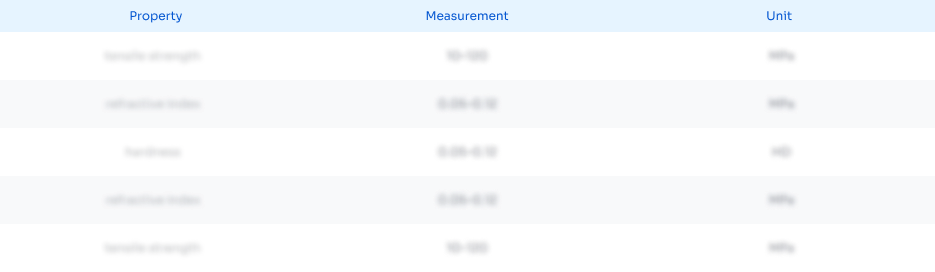
Abstract
Description
Claims
Application Information

- R&D
- Intellectual Property
- Life Sciences
- Materials
- Tech Scout
- Unparalleled Data Quality
- Higher Quality Content
- 60% Fewer Hallucinations
Browse by: Latest US Patents, China's latest patents, Technical Efficacy Thesaurus, Application Domain, Technology Topic, Popular Technical Reports.
© 2025 PatSnap. All rights reserved.Legal|Privacy policy|Modern Slavery Act Transparency Statement|Sitemap|About US| Contact US: help@patsnap.com