High-temperature protective coating for nickel base alloy steel
A high-temperature protection, alloy steel technology, applied in the direction of coating, can solve the problems of difficult and difficult descaling, and achieve the effect of high-temperature protection and descaling, no environmental pollution, and good adhesion performance.
- Summary
- Abstract
- Description
- Claims
- Application Information
AI Technical Summary
Problems solved by technology
Method used
Image
Examples
Embodiment 1
[0016] The weight component of the coating powder is selected as Al 2 o 3 30%, SiO 2 20%, MgO20%, TiO 2 10%, CuO8%, Y 2 o 3 10%, Na 2 O1%, K 2 O1%.
[0017] When using, first mix the powder and water 2:1 to form a slurry. Add binder, binder quality accounts for 10% of slurry quality. A dispersant carboxymethyl cellulose is added, and the quality of the dispersant accounts for 1% of the mass of the slurry.
[0018] The following is a comparative test for the adhesion of 9Ni steel without coating protection and 9Ni steel oxide scale adhesion with coating protection.
[0019] Cut 9Ni steel into 10mm×10mm×10mm samples, anneal in a heating furnace at 700°C and remove surface oil, take it out for later use. Put the surface-coated and non-painted samples into the muffle furnace and heat to 1300°C for one hour.
[0020] figure 1 It is 9Ni steel with coating protection, which is treated at a constant temperature of 1300 ° C for one hour to oxidize the inner layer morphology...
Embodiment 2
[0022] The weight component of the coating powder is selected as Al 2 o 3 35%, SiO 2 15%, MgO15%, TiO 2 18%, CuO8%, Y 2 o 3 7%, Na 2 O1%, K 2 O1%.
[0023] When using, first mix the powder and water 2:1 to form a slurry. Add binder, binder quality accounts for 5% of slurry quality. Add dispersant carboxymethyl cellulose, and the quality of dispersant accounts for 1.5% of the slurry quality.
[0024] The difference between this embodiment and the first embodiment is that the experimental steel type is Q690D (nickel mass fraction is about 0.8%) and the coating composition is different, and the experimental results are the same as the first embodiment.
Embodiment 3
[0026] The weight component of the coating powder is selected as Al 2 o 3 38%, SiO 2 16%, MgO12%, TiO 2 16%, CuO6%, Y 2 o 3 10%, Na 2 O1%, K 2 O1%.
[0027] When using, first mix the powder and water 2:1 to form a slurry. Add binder, binder quality accounts for 8% of slurry quality. Add dispersant carboxymethyl cellulose, and the quality of dispersant accounts for 2% of the slurry quality.
[0028] The difference between this embodiment and the first embodiment is that the experimental steel type is 20Cr2Ni4A (the mass fraction of nickel is about 3.45%) and the coating components are different, and the experimental results are the same as the first embodiment.
PUM
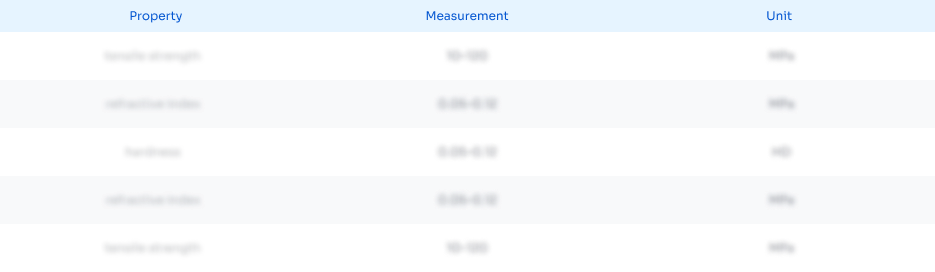
Abstract
Description
Claims
Application Information

- R&D
- Intellectual Property
- Life Sciences
- Materials
- Tech Scout
- Unparalleled Data Quality
- Higher Quality Content
- 60% Fewer Hallucinations
Browse by: Latest US Patents, China's latest patents, Technical Efficacy Thesaurus, Application Domain, Technology Topic, Popular Technical Reports.
© 2025 PatSnap. All rights reserved.Legal|Privacy policy|Modern Slavery Act Transparency Statement|Sitemap|About US| Contact US: help@patsnap.com