High-temperature powder bed system for laser additive manufacture
A laser additive and high-temperature technology, applied in the field of additive manufacturing, can solve the problems of low heating power of the iron core, shorten the service life, and lose heat energy, etc., and achieve the effects of uniform temperature distribution, excellent quality, and uniform heating
- Summary
- Abstract
- Description
- Claims
- Application Information
AI Technical Summary
Problems solved by technology
Method used
Image
Examples
Embodiment Construction
[0020] like figure 1 As shown, the system of the present invention includes a working chamber 10, a laser 1, a workbench 3, an electromagnetic heating layer, a thermal insulation component, a laminar flow uniform temperature component and a cooling channel.
[0021] Workbench 3 can adopt lifting type, is installed in the working cavity 10, specifically can be connected with ball screw 8 by its lower top plate 7, plays the lifting of controlling whole workbench 3. The electromagnetic heating layer is the main heat source, and it is placed on the lower surface of the workbench 3 and tightly attached to it. The heat can be directly conducted to the workbench 3 like this.
[0022] The electromagnetic heating layer is mainly composed of an electromagnetic induction plate 9 and an electromagnetic coil 21 .
[0023] In the actual working process, the working chamber 10 needs to be heated to a very high temperature. In order to protect the additive manufacturing equipment from high ...
PUM
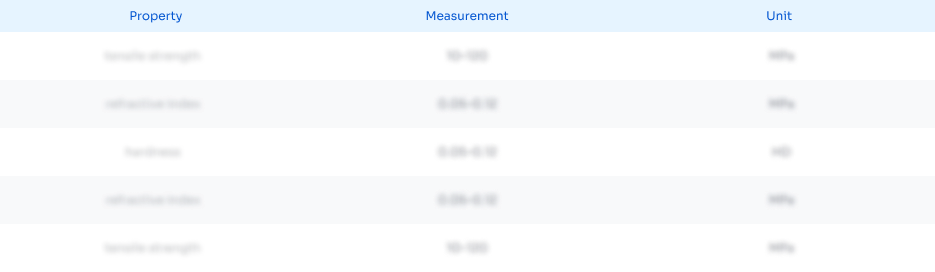
Abstract
Description
Claims
Application Information

- R&D
- Intellectual Property
- Life Sciences
- Materials
- Tech Scout
- Unparalleled Data Quality
- Higher Quality Content
- 60% Fewer Hallucinations
Browse by: Latest US Patents, China's latest patents, Technical Efficacy Thesaurus, Application Domain, Technology Topic, Popular Technical Reports.
© 2025 PatSnap. All rights reserved.Legal|Privacy policy|Modern Slavery Act Transparency Statement|Sitemap|About US| Contact US: help@patsnap.com