A heat treatment process for metallurgical furnace drill rod
A technology for metallurgical furnaces and drill rods, applied in heat treatment furnaces, heat treatment equipment, metal material coating processes, etc., can solve problems such as poor wear resistance, complex working environment of drill rods, and short fatigue life, so as to improve wear resistance The effect of contact fatigue strength, avoiding frequent brittle damage, and improving fatigue life
- Summary
- Abstract
- Description
- Claims
- Application Information
AI Technical Summary
Problems solved by technology
Method used
Examples
Embodiment Construction
[0019] A metallurgical furnace drill rod heat treatment process, comprising the following process steps:
[0020] (1) Carbonitriding. The specific steps of carbonitriding are as follows: use ammonia gas as the nitriding agent and kerosene as the carburizing agent; after the workpiece is loaded, feed ammonia gas at a rate of 2.8 liters per minute until the workpiece comes out of the furnace; after the workpiece is loaded, Control the drop rate of kerosene to 20D / min. When the furnace temperature rises to 930°C, increase the drop rate of kerosene to 65D / min and keep warm for 1 hour; then reduce the drop rate of kerosene to 40D / min and keep warm for 2 hours. Infiltration stage; then lower the furnace temperature to 850°C, drop kerosene to 30D / min, keep warm for 1 hour, this stage is the diffusion stage, and then the workpiece is released from the furnace;
[0021] (2) Use the residual temperature of carbon and nitrogen co-infiltration to spray oil and quench the threaded part of...
PUM
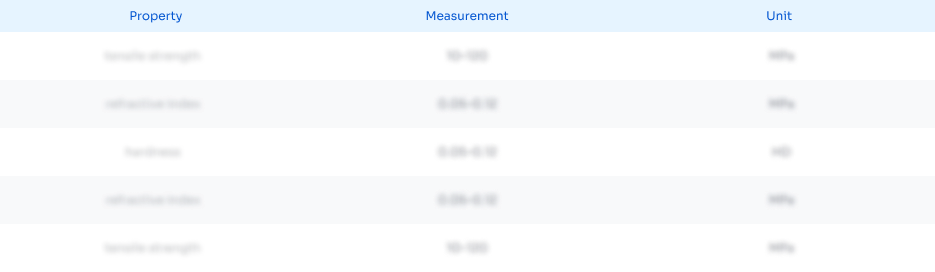
Abstract
Description
Claims
Application Information

- Generate Ideas
- Intellectual Property
- Life Sciences
- Materials
- Tech Scout
- Unparalleled Data Quality
- Higher Quality Content
- 60% Fewer Hallucinations
Browse by: Latest US Patents, China's latest patents, Technical Efficacy Thesaurus, Application Domain, Technology Topic, Popular Technical Reports.
© 2025 PatSnap. All rights reserved.Legal|Privacy policy|Modern Slavery Act Transparency Statement|Sitemap|About US| Contact US: help@patsnap.com