High-thermal-shock-resistance calcium oxide pellet and preparation method thereof
A technology of calcium oxide pellets and thermal shock, which is applied in the direction of solid waste removal, etc., can solve the problems of poor thermal shock resistance of calcium oxide pellets, easy bursting and pulverization, etc., and achieves easy mass production, mature equipment, and mature technology Effect
- Summary
- Abstract
- Description
- Claims
- Application Information
AI Technical Summary
Problems solved by technology
Method used
Image
Examples
Embodiment 1
[0026] The technical solution of the present invention: a calcium oxide pellet with high thermal shock resistance and a preparation method thereof, comprising the following steps:
[0027] (1)Ca(OH) 2Carbide slag powder with a purity greater than 90.0% is ball milled to a particle size of 60.0-150.0 μm, and the mass ratios of the three particle sizes (60-90 μm: 90-120 μm: 120-150 μm) are 4.0: 2.0: 4.0, respectively. The thermal shock resistance of calcium oxide pellets decreases with the increase of carbide slag powder particle size.
[0028] (2) adding 5.0% H to the calcium carbide slag powder pretreated in the step (1) 2 O is used as a binder and mixed evenly, and the thermal shock resistance of calcium oxide pellets increases with the increase of water addition.
[0029] (3) mix and dry the carbide slag powder in the step (2) at 100.0kgf / cm 2 Press molding under the molding pressure and keep the pressure for 0.5min, and dry for 10.0h. When the pressure is 100.0kgf / cm 2...
Embodiment 2
[0033] The technical solution of the present invention: a calcium oxide pellet with high thermal shock resistance and a preparation method thereof, comprising the following steps:
[0034] (1)Ca(OH) 2 Carbide slag powder with a purity greater than 92.4% is ball milled to a particle size of 60.0-150.0 μm, and the mass ratios of the three particle sizes (60-90 μm: 90-120 μm: 120-150 μm) are 4.0:4.0:2.0, respectively. The thermal shock resistance of calcium oxide pellets decreases with the increase of carbide slag powder particle size.
[0035] (2) adding 10.0% H to the calcium carbide slag powder pretreated in the step (1) 2 O is used as a binder and mixed evenly, and the thermal shock resistance of calcium oxide pellets increases with the increase of water addition.
[0036] (3) mix and dry the carbide slag powder in the step (2) at 250.0kgf / cm 2 Press molding under the molding pressure and keep the pressure for 2.5min, and dry for 20.0h. When the pressure is 250.0kgf / cm 2...
Embodiment 3
[0040] The technical solution of the present invention: a calcium oxide pellet with high thermal shock resistance and a preparation method thereof, comprising the following steps:
[0041] (1)Ca(OH) 2 The calcium carbide slag powder with a purity greater than 94.0% is ball milled to a particle size of 60.0-150.0 μm, and the mass ratios of the three particle sizes (60-90 μm: 90-120 μm: 120-150 μm) are 6.0:2.0:2.0, respectively. The thermal shock resistance of calcium oxide pellets decreases with the increase of carbide slag powder particle size.
[0042] (2) adding 15.0% H to the calcium carbide slag powder pretreated in the step (1) 2 O is used as a binder and mixed evenly, and the thermal shock resistance of calcium oxide pellets increases with the increase of water addition.
[0043] (3) Mix and dry the carbide slag powder in the step (2) at 350.0kgf / cm 2 Press molding under the molding pressure and keep the pressure for 3.0min, and dry for 24.0h. When the pressure is 30...
PUM
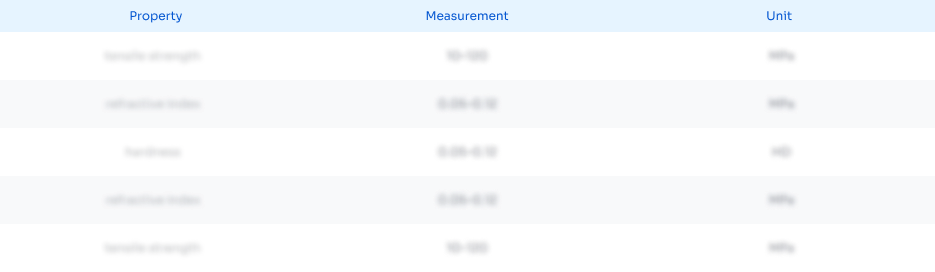
Abstract
Description
Claims
Application Information

- Generate Ideas
- Intellectual Property
- Life Sciences
- Materials
- Tech Scout
- Unparalleled Data Quality
- Higher Quality Content
- 60% Fewer Hallucinations
Browse by: Latest US Patents, China's latest patents, Technical Efficacy Thesaurus, Application Domain, Technology Topic, Popular Technical Reports.
© 2025 PatSnap. All rights reserved.Legal|Privacy policy|Modern Slavery Act Transparency Statement|Sitemap|About US| Contact US: help@patsnap.com