Green cycle production novel method of hydrazine hydrate, hydrazonium salts, and ADC foaming agent
A technology of ADC foaming agent and hydrazine hydrate, which is applied in the field of new green cycle production technology, can solve the problems of waste water pollution, and achieve the effects of low equipment investment, small pressure difference loss, and low energy consumption
- Summary
- Abstract
- Description
- Claims
- Application Information
AI Technical Summary
Problems solved by technology
Method used
Image
Examples
Embodiment 1
[0078] The first step: raw material preparation
[0079] Urea: N%≥46%
[0080] Caustic soda: NaOH%≥30%
[0081] Chlorine: Cl 2 %≥95%
[0082] Catalyst: magnesium chloride hexahydrate, the content is more than 95%
[0083] Slaked Lime: Calcium Hydroxide 95%
[0084] Sodium carbonate decahydrate: Sodium carbonate content is 32%
[0085] The second step: preparation of lime emulsion: add 148kg of slaked lime to 2000 liters of enamel reactor, add 179kg of water and stir to make 327kg of lime milk containing calcium hydroxide 43%.
[0086] The third step: preparation of causticized sodium hypochlorite solution: pour the milk of lime obtained in the first step into the enamel reaction kettle, start stirring, open the jacket frozen brine, add 630 kg of sodium carbonate decahydrate containing 32% sodium carbonate continuously, and simultaneously Continuously feed chlorine gas 133kg and control PH greater than 10, adjust the switch of freezing brine and the amount of chlorine flo...
Embodiment 2
[0095] The first step: raw material preparation
[0096] Urea: N%≥46%
[0097] Caustic soda: NaOH%≥30%
[0098] Chlorine: Cl 2 %≥95%
[0099] Catalyst: magnesium chloride hexahydrate, the content is more than 95%
[0100] Slaked Lime: Calcium Hydroxide 95%
[0101] Sodium carbonate monohydrate: Sodium carbonate content is 67%
[0102] Step 2: Lime emulsion preparation: Add 148kg of slaked lime and 379kg of water into a 2000-liter enamel reactor and stir to make 527kg of lime milk containing 26.7% calcium hydroxide.
[0103] The third step: preparation of causticized sodium hypochlorite solution: add 301 kg of sodium carbonate monohydrate containing 67% sodium carbonate to the milk of lime obtained in the first step, start stirring, and continuously feed 133 kg of chlorine into the sodium carbonate lime emulsion made , and control the pH to be greater than 10, adjust the switch of the frozen brine and the amount of chlorine to control the temperature of the entire reactio...
Embodiment 3
[0110] The first step: raw material preparation
[0111] Urea: N%≥46%
[0112] Caustic soda: NaOH%≥30%
[0113] Chlorine: Cl 2 %≥95%
[0114] Catalyst: magnesium chloride hexahydrate, the content is more than 95%
[0115] Slaked Lime: Calcium Hydroxide 95%
[0116] Sodium sulfate decahydrate: sodium sulfate content is 54% (partial weathering and dehydration)
[0117] Step 2: Lime emulsion preparation: Add 152kg of slaked lime and 318kg of water into a 2000-liter enamel reactor and stir to make 470kg of lime milk containing 30.7% calcium hydroxide.
[0118] The third step: preparation of causticized sodium hypochlorite solution: add sodium sulfate decahydrate 511kg containing sodium sulfate 56% to the milk of lime obtained in the first step, start stirring to make sodium sulfate lime emulsion, and the temperature of the emulsion is lowered to Below 30°C, add chlorine gas to the sodium sulfate lime emulsion, adjust the flow rate of chlorine to control the reaction temperat...
PUM
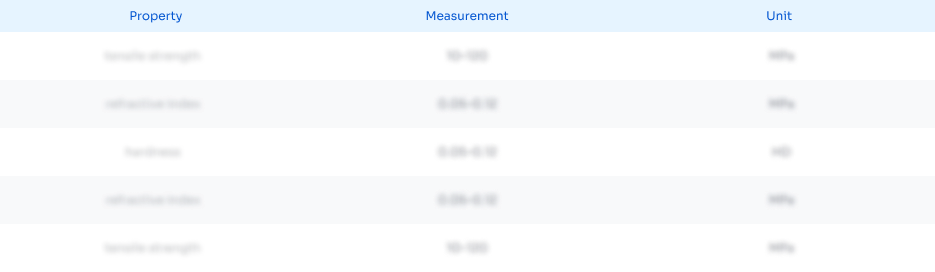
Abstract
Description
Claims
Application Information

- R&D Engineer
- R&D Manager
- IP Professional
- Industry Leading Data Capabilities
- Powerful AI technology
- Patent DNA Extraction
Browse by: Latest US Patents, China's latest patents, Technical Efficacy Thesaurus, Application Domain, Technology Topic, Popular Technical Reports.
© 2024 PatSnap. All rights reserved.Legal|Privacy policy|Modern Slavery Act Transparency Statement|Sitemap|About US| Contact US: help@patsnap.com