Improved preparation method of epoxy trans isoprene rubber
A technology of trans-isoprene rubber and epoxidation, applied in the field of improved epoxidized trans-isoprene rubber preparation, can solve the problems of instability, difficult epoxidation reaction, uneven distribution of epoxy groups, and the like, To achieve the effect of improving adhesion
- Summary
- Abstract
- Description
- Claims
- Application Information
AI Technical Summary
Problems solved by technology
Method used
Examples
Embodiment 1
[0022] Wash and dry a 1000mL three-necked flask, add 150g of toluene solution of trans isoprene rubber, wherein the content of trans isoprene rubber is 30g, start stirring, add 2g of sodium dodecylbenzene sulfonate to dissolve it completely, and then Slowly add 200ml of distilled water, and stir for 30 to 90 minutes at a speed of 800 to 2000 rpm to disperse the copolymerized rubber into an emulsion state; according to organic acid / trans isoprene rubber double bond = 0.8 (molar ratio), hydrogen peroxide / Slowly add acetic acid and hydrogen peroxide to the system at a ratio of organic acid=1.2:1, control the system temperature at 50 degrees, and react for 8 hours. 5 g of methanol was added to perform demulsification. Then it was suction filtered and washed 3 times with distilled water, and weighed after drying. Gained epoxidized trans isoprene rubber was 35g, and its epoxy group content was 71.8% calculated by nuclear magnetic method.
Embodiment 2
[0024] Wash the 50L reactor, add 20000mL of toluene and 2000g of trans isoprene rubber, raise the temperature to 40 degrees and start stirring to dissolve the polymer, according to the organic acid / trans isoprene rubber double bond = 0.4 (molar ratio) 1. Slowly add acetic acid and hydrogen peroxide to the system at a ratio of hydrogen peroxide / organic acid=1.15:1, control the temperature of the system at 40 degrees, and react for 6 hours. After stopping the reaction, the whole system was poured into boiling water, and the solvent was recovered. Then neutralize the polymer slurry with dilute sodium bicarbonate solution to neutrality, filter with suction and wash with distilled water for 3 times, weigh after drying. Gained epoxidized trans isoprene rubber was 2360g, and its epoxy group content was 38.7% calculated by nuclear magnetic method. Performance tests show that the cord pull-out force of epoxidized trans isoprene rubber is 4.87 times higher than that of non-epoxidized t...
Embodiment 3
[0026]Wash and dry a 5000mL three-neck flask, add 2000mL of toluene and 200g of trans isoprene rubber, heat up to 40 degrees and start stirring to dissolve the polymer, according to organic acid / trans isoprene rubber double bond = 0.5 (mol Ratio), hydrogen peroxide / organic acid=1.15:1, slowly add acetic acid and hydrogen peroxide to the system, control the system temperature to 40 degrees, and react for 6 hours. After stopping the reaction, the whole system was poured into boiling water, and the solvent was recovered. Then neutralize the polymer slurry with a dilute sodium hydroxide solution to neutrality, filter it with suction and wash it with distilled water for 3 times, and weigh it after drying. Gained epoxidized trans isoprene rubber was 228g, and its epoxy group content was calculated to be 48.3% by nuclear magnetic method.
PUM
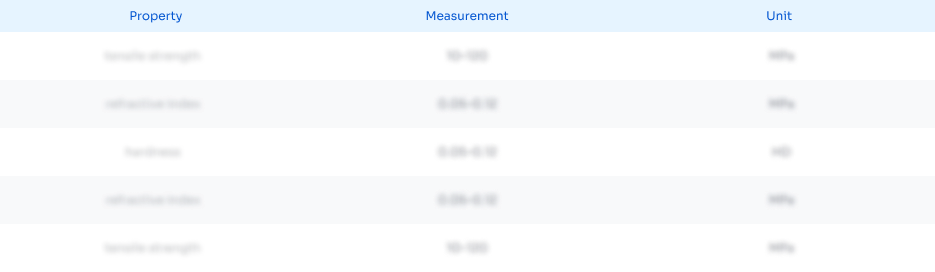
Abstract
Description
Claims
Application Information

- R&D
- Intellectual Property
- Life Sciences
- Materials
- Tech Scout
- Unparalleled Data Quality
- Higher Quality Content
- 60% Fewer Hallucinations
Browse by: Latest US Patents, China's latest patents, Technical Efficacy Thesaurus, Application Domain, Technology Topic, Popular Technical Reports.
© 2025 PatSnap. All rights reserved.Legal|Privacy policy|Modern Slavery Act Transparency Statement|Sitemap|About US| Contact US: help@patsnap.com