Preparation process of epoxy compound
A technology of epoxy compound and preparation process, applied in the direction of organic chemistry, etc., can solve the problems of amplifying safety hazards, unfavorable scale production, and difficulty in realizing scale production.
- Summary
- Abstract
- Description
- Claims
- Application Information
AI Technical Summary
Problems solved by technology
Method used
Image
Examples
preparation example Construction
[0030] A preparation process of an epoxy compound comprises the steps of: reacting an olefin with a halogenating agent in water or a mixed solvent, and then treating with an alkali to obtain an epoxy compound.
[0031] The structural formula of described olefin is as follows:
[0032] ;
[0033] Among them, R 1 or R 2 It is hydrogen or an alkyl group or an aryl group or an alkyl group with a substituent group or an aryl group with a substituent group, and the substituent group is selected from an ether bond, an amide, an ester group, and a mercapto group.
[0034] The mixed solvent is made of water and an organic solvent; the organic solvent is acetonitrile, dichloromethane, ethyl acetate, tetrahydrofuran, dioxane, methanol, ethanol, isopropanol, acetone, methyl ethyl ketone, ether , isopropyl ether, n-butyl ether, methyl tert-butyl ether; preferred mixed solvent is water / acetonitrile mixed solvent.
[0035] The mass of the water or the mixed solvent is 1-20 times the ma...
Embodiment 1
[0043] Add 50 L of water, 5.0 kg of 4,7-dihydro-2,2-dimethyl-1,3-dioxep-5-ene, and 7.6 kg of NBS into the reaction kettle, and stir for 60 minutes. Add 9.6 kg of 50% sodium hydroxide solution dropwise. After the dropwise addition was completed, the mixture was stirred for 1 hour, and then extracted with ethyl acetate. The organic phase was distilled under reduced pressure to obtain 4.1 kg of the product 4,4-dimethyl-3,5,8-trioxabicyclo[5.1.0]octane (purity greater than 97%), with a yield of 75.6%.
Embodiment 2
[0045] Add 20 L of water, 2.5 kg of styrene and 4.7 kg of NBS into the reaction kettle and stir for 30 minutes. Add 5.3 kg of 50% sodium hydroxide solution dropwise, and stir for 1 hour after the addition is completed. Extract with dichloromethane, and distill the organic phase under reduced pressure to obtain 2.0 kg of phenyloxirane (purity greater than 98%), with a yield of 90.1%.
PUM
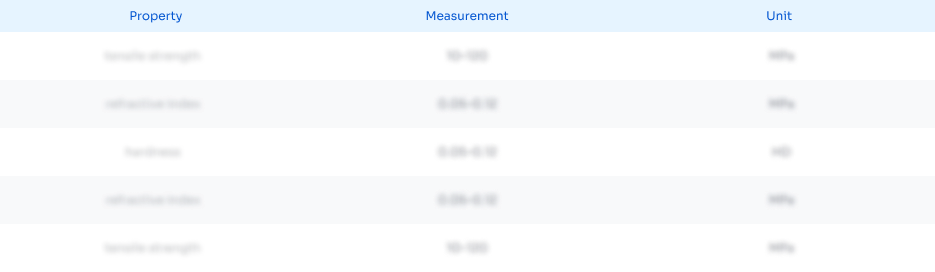
Abstract
Description
Claims
Application Information

- R&D Engineer
- R&D Manager
- IP Professional
- Industry Leading Data Capabilities
- Powerful AI technology
- Patent DNA Extraction
Browse by: Latest US Patents, China's latest patents, Technical Efficacy Thesaurus, Application Domain, Technology Topic, Popular Technical Reports.
© 2024 PatSnap. All rights reserved.Legal|Privacy policy|Modern Slavery Act Transparency Statement|Sitemap|About US| Contact US: help@patsnap.com