Production process for leaching of cobalt from cobalt-containing water-quenched slag
A production process and technology for water quenching slag, applied in the field of production technology of leaching cobalt from water quenching slag, can solve the problems of complicated purification process, large consumption of impurity remover acid, etc.
- Summary
- Abstract
- Description
- Claims
- Application Information
AI Technical Summary
Problems solved by technology
Method used
Examples
Embodiment 1
[0008] The cobalt-containing water-quenched waste slag and pulverized coal produced by a smelter were dried, ground, crushed, and sieved, respectively, and 50g of waste slag fine powder and 3g of fine coal fine powder were weighed, mixed with appropriate amount of water to granulate , Add 1g of lime as binder during the granulation process. After drying, put it into a graphite crucible for roasting, react at a reduction temperature of 800°C for 0.5h to 5h, take it out after the reaction is completed, and cool it at room temperature. Grind the resultant, take 10g of the substance, transfer it to an autoclave, and add ammonium sulfate, sodium peroxodisulfate, ammonia water, water, at an ammonium ammonia ratio of 3, a total ammonia concentration of 10%, a liquid-solid ratio of 5, and a reducing agent The amount of sodium persulfate (multiple of the content of low-priced cobalt) 7. Heat up to 120°C under the condition of continuous stirring. After the reaction, pour cooling water ...
Embodiment 2
[0010] The cobalt-containing water-quenched waste slag and pulverized coal produced by a smelter were dried, ground, crushed, and sieved, respectively, and 50g of waste slag fine powder and 3g of fine coal fine powder were weighed, mixed with appropriate amount of water to granulate , Add 2g of lime as binder during the granulation process. After drying, put it into a graphite crucible for roasting, react at a reduction temperature of 1200°C for 3 hours, take it out after the reaction is completed, and cool it at room temperature. Grind the resultant, take 10g of the substance, transfer it to an autoclave, and add ammonium sulfate, sodium peroxodisulfate, ammonia water, water, at an ammonium ammonia ratio of 4, a total ammonia concentration of 10%, a liquid-solid ratio of 3, and a reducing agent Dosage of sodium persulfate (multiple of low-priced cobalt content) 6. Heat up to 110°C in a sealed environment with constant stirring. After the reaction is completed, pour cooling wa...
Embodiment 3
[0012] The cobalt-containing water-quenched waste slag and pulverized coal produced by a smelter were dried, ground, crushed, and sieved, respectively, and 50g of waste slag fine powder and 3g of fine coal fine powder were weighed, mixed with appropriate amount of water to granulate , Add 1g of lime as binder during the granulation process. After drying, put it into a graphite crucible for roasting, react at a reduction temperature of 1000°C for 2 hours, take it out after the reaction is completed, and cool it at room temperature. Grind the resultant, take 10g of the substance, transfer it to an autoclave, and add ammonium sulfate, sodium peroxodisulfate, ammonia water, water, at an ammonium ammonia ratio of 5, a total ammonia concentration of 8%, a liquid-solid ratio of 3, and a reducing agent Dosage of sodium persulfate (multiple of low-priced cobalt content) 5. Heat up to 130°C in a sealed environment with constant stirring. After the reaction is completed, pour cooling wat...
PUM
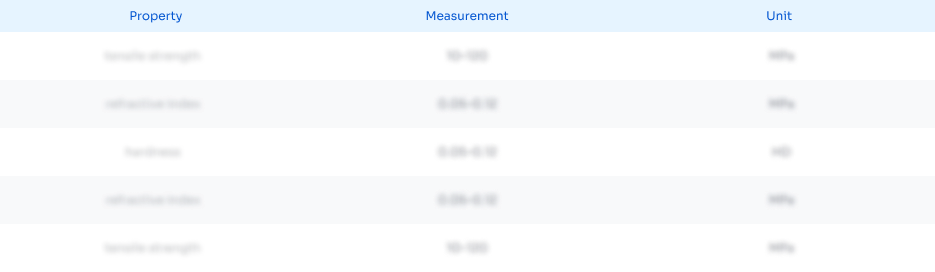
Abstract
Description
Claims
Application Information

- Generate Ideas
- Intellectual Property
- Life Sciences
- Materials
- Tech Scout
- Unparalleled Data Quality
- Higher Quality Content
- 60% Fewer Hallucinations
Browse by: Latest US Patents, China's latest patents, Technical Efficacy Thesaurus, Application Domain, Technology Topic, Popular Technical Reports.
© 2025 PatSnap. All rights reserved.Legal|Privacy policy|Modern Slavery Act Transparency Statement|Sitemap|About US| Contact US: help@patsnap.com