Method for preparing solid lubricant coating on copper base bearing bush
A technology of solid lubricating coating and bearing bush, applied in the direction of coating, lubricating composition, etc., can solve the problems of unsatisfactory lubricating performance, copper adhesion and insufficient wear resistance, improve emergency operation ability and service life, and solve the problem of wear resistance. Insufficient abrasiveness, good bonding effect
- Summary
- Abstract
- Description
- Claims
- Application Information
AI Technical Summary
Problems solved by technology
Method used
Image
Examples
Embodiment 1
[0023] Weigh 100 grams of molybdenum disulfide, 20 grams of graphite, 10 grams of hexagonal boron nitride, 15 grams of cerium trifluoride, 35 grams of antimony trioxide and 5 grams of organic silicon resin into a grinding jar, add 100 grams of organic solvent for Grind and disperse; add 215 grams of polyamideimide and 650 grams of organic solvents again, stir to obtain solid lubricating coating (organic solvent is that N-methylpyrrolidone and aromatic hydrocarbon solvent mix by weight 3:1); The paint is evenly sprayed on the surface of the copper base of the metal bearing, and it is left to stand for 10-30 minutes to dry, then placed in an oven, kept at 280±10°C for 2-3 hours, and cooled to obtain a solid lubricating coating on the surface of the copper-based bearing.
Embodiment 2
[0025] Molybdenum disulfide 6.0%, graphite 3.0%, hexagonal boron nitride 2.0%, cerium trifluoride 1.5%, antimony trioxide 5.0%, polyamideimide 15.0%, polytetrafluoroethylene 2.0%, silicone resin 0.8 %, organic solvent balance (N-methylpyrrolidone and acetanilide are mixed by weight 3:1); method is the same as in Example 1.
Embodiment 3
[0027] Molybdenum disulfide 3.0%, graphite 2.0%, hexagonal boron nitride 3.0%, cerium trifluoride 0.7%, antimony trioxide 5.0%, polyamideimide 17.0%, polytetrafluoroethylene 5.0%, silicone resin 0.1 %, organic solvent balance (N-methylpyrrolidone and methylene chloride are mixed by weight 1:1.5); method is the same as in Example 1.
PUM
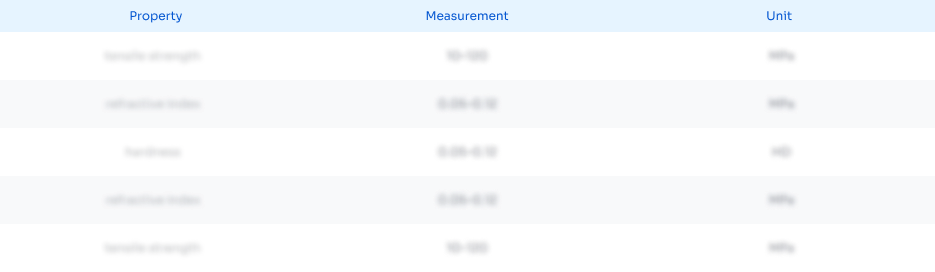
Abstract
Description
Claims
Application Information

- R&D Engineer
- R&D Manager
- IP Professional
- Industry Leading Data Capabilities
- Powerful AI technology
- Patent DNA Extraction
Browse by: Latest US Patents, China's latest patents, Technical Efficacy Thesaurus, Application Domain, Technology Topic, Popular Technical Reports.
© 2024 PatSnap. All rights reserved.Legal|Privacy policy|Modern Slavery Act Transparency Statement|Sitemap|About US| Contact US: help@patsnap.com