Preparation method for low-color number environment-friendly polyurethane curing agent
A polyurethane curing agent, an environmentally friendly technology, applied in the chemical industry, sustainable manufacturing/processing, climate sustainability, etc., can solve problems such as prolonged reaction time, stable removal of free monomers, and complicated and difficult recycling processes. Achieve the effects of stable reaction temperature control, improved TDI utilization, and excellent storage stability
- Summary
- Abstract
- Description
- Claims
- Application Information
AI Technical Summary
Problems solved by technology
Method used
Examples
Embodiment 1
[0033] The reactor adopts a continuous series of four-stage stirred reactors. At 25°C, TDI (2,4-TDI content is 65%) and diethylene glycol are continuously added to the first reaction kettle at a mass ratio of 88:3, and the temperature is gradually raised to 55°C and maintained at 30-55°C. The residence time is 30min, and the reaction liquid of the first reactor is obtained; TMP and the reaction liquid of the first reactor are added into the second reactor according to the mass ratio of 6:91 for reaction, and the temperature is slowly raised from 55°C to 65°C. By adjusting the flow of condensed water to control the reaction temperature to maintain at 55 ~ 65 ° C, the residence time is 1h, to obtain the reaction liquid of the second reactor; the remaining TMP and the reaction liquid of the second reactor are added to the second reaction tank according to the mass ratio of 3:97. The reaction is carried out in the three reactors, relying on the residual heat of the reaction, the r...
Embodiment 2
[0035] The reactor adopts a continuous series of four-stage stirred reactors. At 25°C, TDI (2,4-TDI content 67%), methylpropanediol, and 1,3-butanediol were continuously added to the first reactor at a mass ratio of 88:2:1, and the temperature was gradually raised to 55 ℃, at this time maintained at 30 ~ 55 ℃, the residence time is 50min, the reaction liquid of the first reactor is obtained; Slowly heat up from 55°C to 65°C, the reaction temperature can be controlled by adjusting the flow of condensed water to maintain the temperature at 55°C ~ 65°C, and the residence time is 70min to obtain the reaction liquid in the second reactor; the remaining TMP and the reaction liquid in the second reactor are according to The ratio of 4:96 is added to the third reactor for reaction, the reaction temperature is maintained at 65-75°C, and the residence time is 50min to obtain the third reactor reaction liquid; then the third reactor reaction liquid enters the fourth reactor, Maintain th...
Embodiment 3
[0037] The reactor adopts a continuous series of four-stage stirred reactors. At 25°C, TDI (2,4-TDI content 62%) and 1,3-propanediol are continuously added to the first reaction kettle at a mass ratio of 88.5:3.5, and the temperature gradually rises to 55°C, and is maintained at 30~ 55°C, the residence time is 40min, and the reaction liquid of the first reactor is obtained; TMP and the reaction liquid of the first reactor are added into the second reactor according to the mass ratio of 6:92 for reaction, and the temperature is slowly raised from 55°C to 65 °C, the reaction temperature can be controlled by adjusting the flow of condensed water to maintain the temperature at 55-65 °C, and the residence time is 1.5h to obtain the reaction liquid in the second reactor; the remaining TMP and the reaction liquid in the second reactor are based on the mass ratio of 2:98 The ratio is added to the third reactor for reaction, relying on the residual heat of the reaction, the reaction te...
PUM
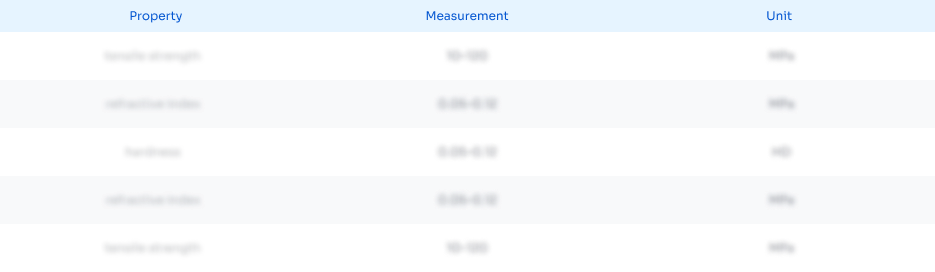
Abstract
Description
Claims
Application Information

- Generate Ideas
- Intellectual Property
- Life Sciences
- Materials
- Tech Scout
- Unparalleled Data Quality
- Higher Quality Content
- 60% Fewer Hallucinations
Browse by: Latest US Patents, China's latest patents, Technical Efficacy Thesaurus, Application Domain, Technology Topic, Popular Technical Reports.
© 2025 PatSnap. All rights reserved.Legal|Privacy policy|Modern Slavery Act Transparency Statement|Sitemap|About US| Contact US: help@patsnap.com