Micro-nano intragranular multiphase granule and thermal explosion reaction synthetic method thereof
A thermal explosion reaction, micro-nano technology, applied in the field of micro-nano composite materials and their synthesis, micro-nano intracrystalline multi-phase particles and their thermal explosion reaction synthesis method, can solve the problems of poor toughness, high brittleness, etc., and achieve improved performance , Improve toughness and high bonding strength
- Summary
- Abstract
- Description
- Claims
- Application Information
AI Technical Summary
Problems solved by technology
Method used
Image
Examples
Embodiment 1
[0031] Example 1: Al-TiO 2 -B 2 o 3 reaction system
[0032] (1) Preparation of reaction samples Al powder, TiO 2 Powder and B 2 o 3 The molar ratio of the powder is 10:1:1, and then they are put into a ball mill tank, mixed with a ball-to-powder ratio of 5:1, and a speed of 300p.r.m, and then extruded into a billet with a pressure of 120MPa to make a compact. Sample;
[0033] (2) Loading and vacuuming the compacted sample into the vacuum reaction furnace, and vacuuming to 10 -4 -10 -3 Pa;
[0034] (3) Reaction synthesis Adjust the input power, the heating rate is 20K / min and the temperature rises to 900°C for the compacted sample to undergo a chemical reaction;
[0035] (4) Heat preservation Once the chemical reaction of the reaction sample occurs, the input power can be lowered, and the power input can be stopped after 30 minutes of heat preservation.
[0036] (5) Cool down and take out the furnace. When the furnace is cooled to room temperature, the furnace is o...
Embodiment 2
[0042] Example 2: Al-TiO 2 -B 2 o 3 reaction system
[0043] (1) Preparation of reaction samples Al powder, TiO 2 Powder and B 2 o 3 The molar ratio of the powder is 12:1:1, and then they are put into a ball mill tank, ball milled and mixed at a ball powder ratio of 4.5:1 at a speed of 280p.r.m, and then extruded into a billet with a pressure of 120MPa to make a compact. Sample;
[0044] (2) Loading and vacuuming the compacted sample into the vacuum reaction furnace, and vacuuming to 10 -4 -10 -3 Pa;
[0045] (3) Reaction synthesis Adjust the input power, raise the temperature at a heating rate of 18K / min, and the chemical reaction will occur in the compacted sample at 880°C;
[0046] (4) Heat preservation Once the chemical reaction of the reaction sample occurs, the input power can be lowered, and the power input can be stopped after 50 minutes of heat preservation.
[0047] (5) Cool down and take out the furnace. When the furnace is cooled to room temperature, th...
Embodiment 3
[0052] Example 3: Al-TiO 2 -B 2 o 3 reaction system
[0053] (1) Preparation of reaction samples Al powder, TiO 2 Powder and B 2 o 3 The molar ratio of the powder is 17:1:1, and then they are put into a ball mill tank, mixed with a ball powder ratio of 5:1, 300p.r.m speed of ball milling, and then extruded into a billet with a pressure of 120MPa to make a green compact. Sample;
[0054] (2) Loading and vacuuming the compacted sample into the vacuum reaction furnace, and vacuuming to 10 -4 -10 -3 Pa;
[0055] (3) Reaction synthesis Adjust the input power, heat up at a heating rate of 15K / min, and the compacted sample undergoes a chemical reaction at 860°C;
[0056] (4) Heat preservation Once the chemical reaction of the reaction sample occurs, the input power can be lowered, and the power input can be stopped after 60 minutes of heat preservation.
[0057] (5) Cool down and take out the furnace. When the furnace is cooled to room temperature, the furnace is opened f...
PUM
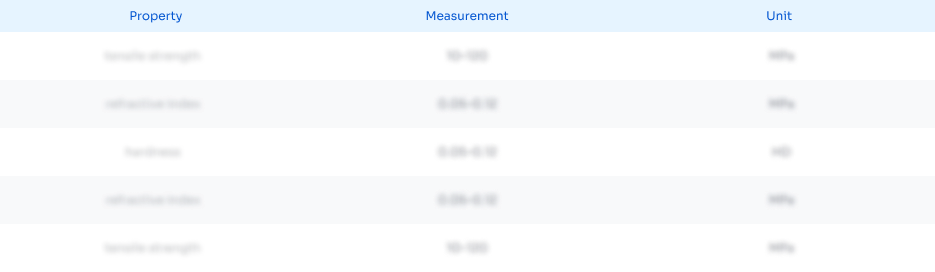
Abstract
Description
Claims
Application Information

- R&D Engineer
- R&D Manager
- IP Professional
- Industry Leading Data Capabilities
- Powerful AI technology
- Patent DNA Extraction
Browse by: Latest US Patents, China's latest patents, Technical Efficacy Thesaurus, Application Domain, Technology Topic, Popular Technical Reports.
© 2024 PatSnap. All rights reserved.Legal|Privacy policy|Modern Slavery Act Transparency Statement|Sitemap|About US| Contact US: help@patsnap.com