Composite environment-friendly fireproof board
A fireproof board, an environmentally friendly technology, applied in the field of building boards, can solve the problems of high cost, long curing time, etc., and achieve the effect of good fire resistance
- Summary
- Abstract
- Description
- Claims
- Application Information
AI Technical Summary
Problems solved by technology
Method used
Image
Examples
Embodiment 1
[0007] Composition ratio
[0008]
[0009] Among them, the magnesium-aluminum composite cementitious material is made by stirring and mixing uniformly 40 kg of light-burned magnesium oxide (Mg0 > 80%), 30 kg of brine, 3 kg of aluminate cement, and 5 kg of talcum powder.
[0010] Mix the magnesium-aluminum composite cementitious material with hollow floating beads, expanded vermiculite, rice straw, fly ash, and silica fume evenly, then add sodium dihydrogen phosphate and boric acid to stir and mix, add and adjust to formable materials, pour into molding, and maintain In 7 days, the present invention was obtained. Its performance indicators are shown in Table 1.
Embodiment 2
[0012] Composition ratio
[0013]
[0014] Among them, the magnesium-aluminum composite cementitious material is prepared by stirring and mixing uniformly 45 kg of light-burned magnesium oxide (Mgo>80%), 32 kg of brine, 2 kg of aluminate cement, and 1 kg of talcum powder.
[0015] After the magnesium-aluminum composite gelling material is uniformly mixed with expanded vermiculite, wheat straw, fly ash, and water glass, phosphoric acid and boric acid are added to stir and mix, water is added to adjust to become a material, casting is formed, and the invention is obtained by curing for 10 days. Its performance indicators are shown in Table 1.
Embodiment 3
[0017] Group ratio
[0018]
[0019]
[0020] Among them, the magnesium-aluminum composite cementitious material is prepared by stirring and mixing uniformly 42 kg of light-burned magnesium oxide (Mg0>80%), 30 kg of brine, 5 kg of aluminate cement, and 2 kg of talcum powder.
[0021] Mix the magnesium-aluminum composite cementitious material with hollow floating beads, expanded vermiculite, rice straw, fly ash, and alumina evenly, then add aluminum phosphate and 8291 unsaturated polyester resin to mix, add water to adjust to a moldable material, and cast to form , the present invention was obtained after 8 days of maintenance.
PUM
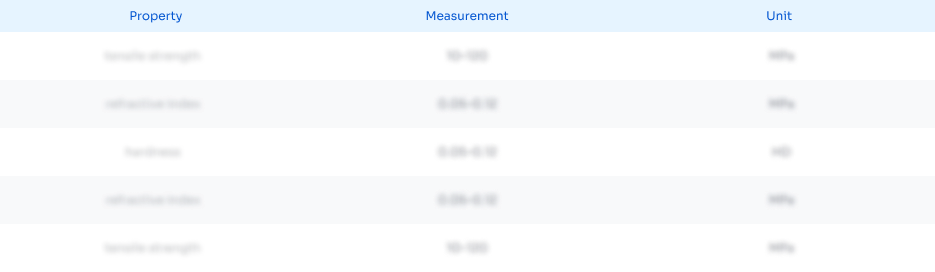
Abstract
Description
Claims
Application Information

- R&D
- Intellectual Property
- Life Sciences
- Materials
- Tech Scout
- Unparalleled Data Quality
- Higher Quality Content
- 60% Fewer Hallucinations
Browse by: Latest US Patents, China's latest patents, Technical Efficacy Thesaurus, Application Domain, Technology Topic, Popular Technical Reports.
© 2025 PatSnap. All rights reserved.Legal|Privacy policy|Modern Slavery Act Transparency Statement|Sitemap|About US| Contact US: help@patsnap.com