Disperse dye ink for cotton fabric inkjet printing and preparation method thereof
A disperse dye, inkjet printing technology, applied in the fields of fine chemicals and material science, can solve the problems of low affinity of cotton fibers, low molecular weight, affecting the moisture absorption and air permeability of printed fabrics, etc., achieve high brightness, solve waste paper, fastness Good results
- Summary
- Abstract
- Description
- Claims
- Application Information
AI Technical Summary
Problems solved by technology
Method used
Examples
example 1
[0018] The parts by weight are 5 parts of C. I. Disperse Red 60 and 1 part of co-emulsifier hexadecane are dispersed in 70 parts of styrene to form the oil phase, and 0.5 parts of emulsifier polyoxyethylene sorbitan monooleate is dissolved in deionized water to form the water phase , Disperse 10 parts of the oil phase into the water phase under stirring, emulsify at high speed and place it in an ultrasonic cell pulverizer for 5 minutes to make an O / W type fine emulsion. Transfer the O / W type miniemulsion to a four-necked flask equipped with a stirrer, a reflux condenser and a thermometer, keep the stirring speed at 100r / min, blow nitrogen for 10min, raise the temperature to 50°C and add 20g of potassium persulfate dissolved in 0.35g The aqueous solution initiates polymerization, and after reacting for 1 hour, the mixture is cooled and discharged, and filtered with 500 nanometer microporous filter paper to remove impurities to obtain latex particle nanocomposite pigment, which...
example 2
[0021] Disperse Red 65 and 10 parts of co-emulsifier hexadecane in parts by weight are dispersed in 95 parts of styrene to form an oil phase, and 5 parts of emulsifiers are dissolved in deionized water to form a water phase, Disperse 40 parts of the oil phase into the water phase under stirring, emulsify at a high speed, and place it in an ultrasonic cell pulverizer for 30 minutes to make an O / W type fine emulsion. Transfer the O / W type miniemulsion to a four-neck flask equipped with a stirrer, reflux condenser and thermometer, keep the stirring speed at 1000r / min, blow nitrogen for 60min, raise the temperature to 80°C and add 20g of aqueous solution containing 1g of ammonium persulfate Initiate polymerization, react for 4 hours, cool and discharge, filter with 500nm microporous filter paper to remove impurities to obtain latex particle nano-composite pigment, set aside. Add 50 parts of latex particle nanocomposite pigment, 35 parts of n-propanol and polyethylene glycol 600 mi...
example 3
[0024] Parts by weight are 15 parts of C.I, disperse yellow 7 and 5 parts of co-emulsifier cetyl mercaptan are dispersed in 80 parts of butadiene to form an oil phase, and 4 parts of emulsifier sodium lauryl sulfate Dissolve in deionized water to form the water phase, disperse 30 parts of the oil phase into the water phase under stirring, emulsify at high speed and place it in an ultrasonic cell pulverizer for 25 minutes to make an O / W type fine emulsion. Transfer the O / W type miniemulsion to a four-necked flask equipped with a stirrer, a reflux condenser and a thermometer, keep the stirring speed at 500r / min, blow nitrogen for 50min, raise the temperature to 70°C and add 20g of azobisiso Butyamidine hydrochloride aqueous solution initiates polymerization, reacts for 3 hours, cools and discharges, and filters with 500 nanometer microporous filter paper to remove impurities to obtain latex particle nanocomposite pigment, which is ready for use. Add 40 parts of latex particle na...
PUM
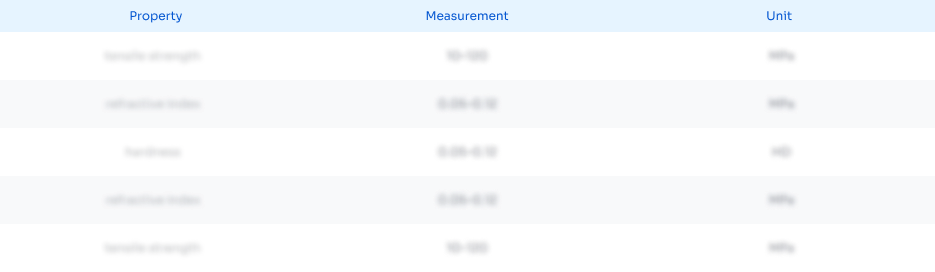
Abstract
Description
Claims
Application Information

- R&D Engineer
- R&D Manager
- IP Professional
- Industry Leading Data Capabilities
- Powerful AI technology
- Patent DNA Extraction
Browse by: Latest US Patents, China's latest patents, Technical Efficacy Thesaurus, Application Domain, Technology Topic, Popular Technical Reports.
© 2024 PatSnap. All rights reserved.Legal|Privacy policy|Modern Slavery Act Transparency Statement|Sitemap|About US| Contact US: help@patsnap.com