Si-Al-O-N-B multiphase ceramic material and preparation method thereof
A technology for multiphase ceramics and raw materials, applied in the field of functional ceramics, can solve the problems of high dielectric constant, difficult to form complex components, limited purity, etc., and achieve the effects of not easy to crack, solve rheological properties, and reduce dielectric constant.
- Summary
- Abstract
- Description
- Claims
- Application Information
AI Technical Summary
Problems solved by technology
Method used
Image
Examples
Embodiment 1
[0030] The Si-Al-O-N-B composite ceramic material of this embodiment is pressed into a green body from the following raw materials and mixed powder in parts by weight: 100g of silicon nitride, 50g of aluminum nitride, and 55g of aluminum oxide; Oxyzine is impregnated into the green body, then cross-linked and solidified, pyrolyzed at high temperature, and sintered; its dielectric constant is 4.73.
[0031] preparation:
[0032] (1) Forming of the biscuit: Mix 100g of silicon nitride (particle size 0.5μm), 50g of aluminum nitride (particle size of 0.8μm), and 55g of alumina (particle size of 1.0μm) in a uniform ratio, ball mill for 24 hours, and then use The mixed powder is pressed into shape by a mechanical compression molding method, and the molding pressure is 150 MPa.
[0033] (2) Immerse borazine, the liquid precursor of BN, into the green body by vacuum impregnation (initial pressure: 100Pa). Make the precursor fully infiltrate into the biscuit.
[0034] (3) Place the ...
Embodiment 2
[0037] In this embodiment, the Si-Al-O-N-B composite ceramic material is pressed into a green body from the following raw materials and mixed powder in parts by weight: 60 g of silicon nitride, 80 g of aluminum nitride, 20 g of aluminum oxide, and 40 g of silicon oxide; The liquid precursor borazine is impregnated into the green body, then cross-linked and solidified, cracked at high temperature and sintered; its dielectric constant is 3.55.
[0038] preparation:
[0039] (1) Forming of the biscuit: Mix 60g of silicon nitride (particle size 100nm), 80g of aluminum nitride (particle size of 200nm), 20g of alumina (particle size of 80nm), 40g of silicon oxide (particle size of 200nm), and ball mill After 12 hours, the mixed powder was prepared by gel injection molding.
[0040] (2) Immerse borazine, the liquid precursor of BN, into the biscuit by means of pressure impregnation. The body is fully infiltrated into the biscuit; the pressure is 5MPa, and the medium is nitrogen.
...
Embodiment 3
[0044]In this embodiment, the Si-Al-O-N-B composite ceramic material is pressed into a green body from the following raw materials and mixed powder in parts by weight: 50 g of silicon nitride, 40 g of aluminum nitride, 50 g of aluminum oxide, and 60 g of silicon oxide; The liquid precursor borazine is impregnated into the green body, then cross-linked and solidified, pyrolyzed at high temperature, and sintered; its dielectric constant is 4.41.
[0045] preparation:
[0046] (1) Forming of the biscuit: Mix 50g of silicon nitride (particle size 10μm), 40g of aluminum nitride (particle size of 5μm), 50g of alumina (particle size of 3 μm), and 60g of silicon oxide (particle size of 2μm), After ball milling for 30 hours, the mixed powder was prepared by cold isostatic pressing at a pressure of about 240 MPa.
[0047] (2) Immerse borazine, the liquid precursor of BN, into the green body by means of pressure impregnation. 2MPa, stand still for 5h, so that the borazine precursor ful...
PUM
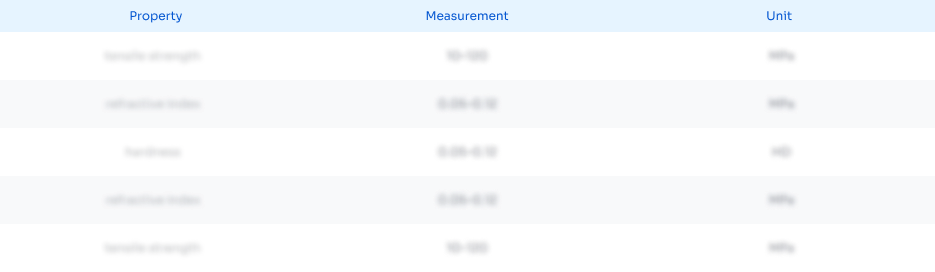
Abstract
Description
Claims
Application Information

- R&D Engineer
- R&D Manager
- IP Professional
- Industry Leading Data Capabilities
- Powerful AI technology
- Patent DNA Extraction
Browse by: Latest US Patents, China's latest patents, Technical Efficacy Thesaurus, Application Domain, Technology Topic, Popular Technical Reports.
© 2024 PatSnap. All rights reserved.Legal|Privacy policy|Modern Slavery Act Transparency Statement|Sitemap|About US| Contact US: help@patsnap.com