Production method of high-performance fiber composite product
A high-performance fiber and composite material technology, applied in other household appliances, household appliances, household components, etc., can solve the problems of high manufacturing cost, poor impact toughness, heavy material, etc., and achieve low manufacturing cost and strong impact toughness. , the effect of light material
- Summary
- Abstract
- Description
- Claims
- Application Information
AI Technical Summary
Problems solved by technology
Method used
Examples
Embodiment 1
[0013] Step 1: Cut 2-3 layers of high-strength glass fiber plain weave fabric or multi-axial warp-knitted fabric according to the specifications of composite material products, and lay them together;
[0014] Step 2: Cut 3-5 layers of high-strength carbon fiber plain fabric or multi-axial warp knitted fabric according to the specifications of the composite material product, and lay them together;
[0015] Step 3: Cut 2-3 layers of high-strength and high-modulus polyethylene fiber plain fabrics that have been treated with surface plasma according to the specifications of composite materials, and lay them together;
[0016] Step 4: Cut 2-3 layers of high-strength glass fiber plain weave fabric or multiaxial warp-knitted fabric according to the specifications of the composite material, and lay them together;
[0017] The three high-performance fiber fabrics used in the above steps 1 to 4, 160g to 250g per square meter;
[0018] Step 5: Finally, lay the fabrics of Step 1, Step 2,...
Embodiment 2
[0020] Step 1: Cut high-strength glass fiber plain weave or multi-axial warp knitted fabric according to the specifications of composite material products and lay them together in 2 to 3 layers;
[0021] Step 2: Cut high-strength carbon fiber plain weave fabric or multi-axial warp knitted fabric according to the specifications of composite material products and lay them together in 3 to 5 layers;
[0022] Step 3: Cut the high-strength and high-modulus polyethylene fiber plain weave fabric that has been treated with surface plasma, and lay it together in 2 to 3 layers according to the specifications of the composite material product;
[0023] Step 4: Cut the high-strength glass fiber plain weave fabric or multi-axial warp knitted fabric according to the specifications of the composite materials and lay them together in 2 to 3 layers;
[0024] The three high-performance fiber fabrics used in the above steps 1 to 4, 160g to 250g per square meter;
[0025] Step 5: Finally, lay th...
PUM
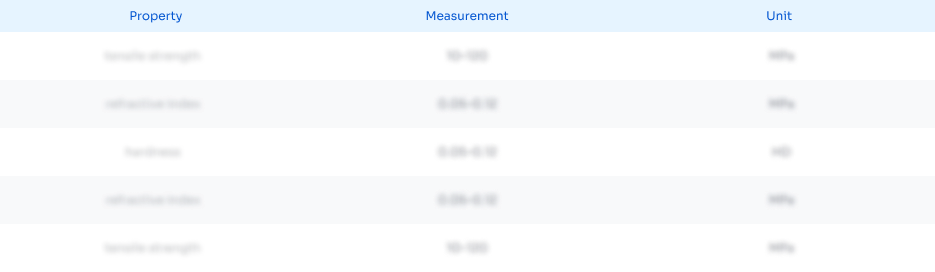
Abstract
Description
Claims
Application Information

- R&D
- Intellectual Property
- Life Sciences
- Materials
- Tech Scout
- Unparalleled Data Quality
- Higher Quality Content
- 60% Fewer Hallucinations
Browse by: Latest US Patents, China's latest patents, Technical Efficacy Thesaurus, Application Domain, Technology Topic, Popular Technical Reports.
© 2025 PatSnap. All rights reserved.Legal|Privacy policy|Modern Slavery Act Transparency Statement|Sitemap|About US| Contact US: help@patsnap.com