Preparation method of catalyst for hydro-treatment
A hydrogenation treatment and catalyst technology, applied in the direction of physical/chemical process catalysts, catalyst carriers, chemical instruments and methods, etc., can solve problems such as environmental pollution, low sodium content, large amounts of waste water, etc., and achieve no environmental pollution, acidity improvement, The effect of concentrated hole distribution
- Summary
- Abstract
- Description
- Claims
- Application Information
AI Technical Summary
Problems solved by technology
Method used
Image
Examples
Embodiment 1
[0037] Fully mix 200g of kaolin raw soil with 40mL of 3.0mol / L acetic acid, 20mL of 0.5mol / L citric acid and 16g of polyethylene glycol dissolved in 40mL of water, and carry out modification treatment on a hydrothermal treatment device. The hydrothermal treatment temperature is 650°C. 5h, hydrothermal treatment pressure 0.27MPa. The processed kaolin is cooled and pulverized through a 160-mesh sieve and collected for use.
[0038] Preparation of sodium metaaluminate solution concentration is 50gAl 2 o 3 / L, a total of 1L, heated to 70°C for use, the concentration of aluminum sulfate solution is 20gAl 2 o 3 / L for a total of 2L, heated to 75°C for use.
[0039] Add 1.0L of distilled water and 45g of the above-mentioned modified kaolin into the gelling tank, and heat to 75°C. Take by weighing 45g of the above-mentioned modified kaolin and put it in the aluminum sulfate solution, and add aluminum sulfate and sodium metaaluminate solution to keep the pH value at 7.5, and the s...
Embodiment 2
[0045] The preparation method of the carrier and the catalyst is the same as in Example 1, and the carrier B and the catalyst T-B are prepared.
[0046] Example 3
Embodiment 3
[0048] Weigh 100g of the prepared silicon-containing alumina dry glue (73wt% silicon-containing alumina), add 1.46g of turnip powder and mix evenly, add 4.06g of acetic acid diluted with 95g of distilled water to the mixed raw materials, knead and extrude into strips, Then it was dried at 110°C for 4h and calcined at 800°C for 3h to obtain carrier C.
[0049] Weigh 20.78g of phosphoric acid, add 400mL of distilled water, then sequentially add 45.14g of molybdenum oxide and 14.44g of basic nickel carbonate, heat and stir until completely dissolved, then adjust the solution to 500mL with distilled water to obtain solution L-2. Saturatedly impregnate the above-mentioned carrier with the L-2 solution, dry at 120°C for 2 hours, and calcinate at 480°C for 5 hours to obtain catalyst T-C.
[0050] Example 4
PUM
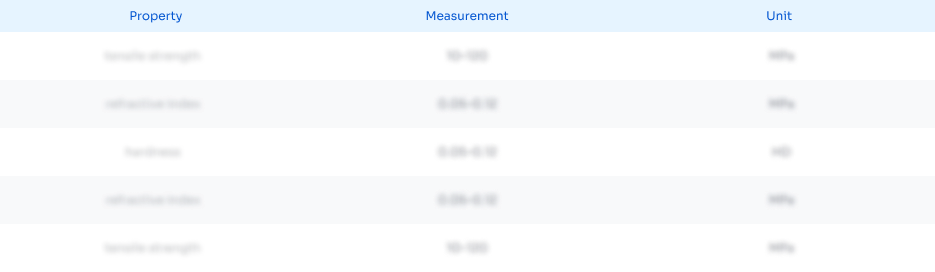
Abstract
Description
Claims
Application Information

- R&D
- Intellectual Property
- Life Sciences
- Materials
- Tech Scout
- Unparalleled Data Quality
- Higher Quality Content
- 60% Fewer Hallucinations
Browse by: Latest US Patents, China's latest patents, Technical Efficacy Thesaurus, Application Domain, Technology Topic, Popular Technical Reports.
© 2025 PatSnap. All rights reserved.Legal|Privacy policy|Modern Slavery Act Transparency Statement|Sitemap|About US| Contact US: help@patsnap.com