High-power LED chip making method
An LED chip and manufacturing method technology, applied in electrical components, circuits, semiconductor devices, etc., can solve the problems of high packaging thermal resistance, low light extraction efficiency, and high cost, and achieve the goal of reducing packaging thermal resistance, improving light extraction efficiency, and reducing costs. Effect
- Summary
- Abstract
- Description
- Claims
- Application Information
AI Technical Summary
Problems solved by technology
Method used
Examples
Embodiment 1
[0019] A method for manufacturing a high-power LED chip, characterized in that: comprising the following steps:
[0020] Step 1: LED chip inspection Microscopic inspection: whether there is mechanical damage and pitting on the surface of the material, whether the chip size and electrode size meet the process requirements, and whether the electrode pattern is complete;
[0021] Step 2: Expand the film bonded to the chip with a chip expander, so that the distance between the LED chips is stretched to about 0.6mm;
[0022] Step 3: LED dispensing, apply silver glue or insulating glue on the corresponding position of the LED bracket;
[0023] Step 4: LED glue preparation, glue preparation is to use the glue preparation machine to first apply silver glue on the back electrode of the LED, and install the LED with silver glue on the back of the LED bracket, the efficiency of glue preparation is much higher than dispensing;
[0024] Step 5: LED manual stabbing. Place the expanded LED ...
PUM
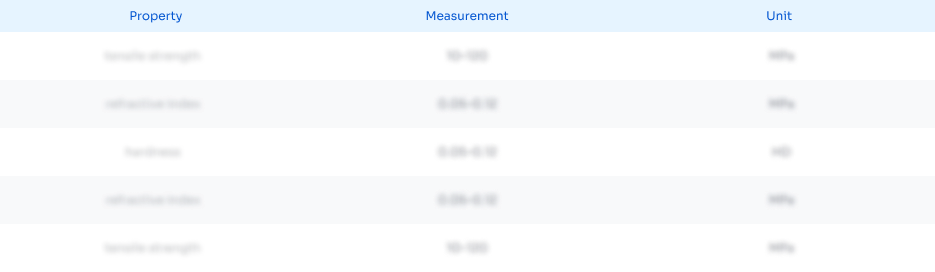
Abstract
Description
Claims
Application Information

- Generate Ideas
- Intellectual Property
- Life Sciences
- Materials
- Tech Scout
- Unparalleled Data Quality
- Higher Quality Content
- 60% Fewer Hallucinations
Browse by: Latest US Patents, China's latest patents, Technical Efficacy Thesaurus, Application Domain, Technology Topic, Popular Technical Reports.
© 2025 PatSnap. All rights reserved.Legal|Privacy policy|Modern Slavery Act Transparency Statement|Sitemap|About US| Contact US: help@patsnap.com