Single-substrate multi-chipset high-power LED (Light-Emitting Diode) encapsulation one-step bonding method
An LED packaging, multi-chip technology, applied in electrical components, electrical solid devices, circuits, etc., can solve problems such as long bonding time, improve packaging efficiency, enhance heat dissipation, and improve the rate of qualified products
- Summary
- Abstract
- Description
- Claims
- Application Information
AI Technical Summary
Problems solved by technology
Method used
Image
Examples
specific Embodiment approach 1
[0019] Specific implementation mode one: the following combination Figure 1 to Figure 6 Describe this implementation mode, this implementation mode comprises the following steps:
[0020] Step 1: cleaning the substrate 1, the slide table 2, the multi-chip nozzle 3 and the support table 4;
[0021] Step 2: Place the substrate 1 on the support table 4; determine the position of the chip to be bonded on the front of the substrate 1, and place a plurality of chips 5 to be bonded on the carrier according to the arrangement corresponding to the position of the chip to be bonded on stage 2;
[0022] Step 3: uniformly apply the solder paste on the positions of the chips to be bonded by screen printing, and then use the multi-chip suction nozzle 3 to simultaneously pick up multiple chips 5 to be bonded;
[0023] Step 4: Use a heat source to heat the back of the substrate 1, align the multiple chips 5 to be bonded picked up by the multi-chip suction nozzle 3 to the position to be bon...
specific Embodiment approach 2
[0026] Embodiment 2: This embodiment is a further description of Embodiment 1, and the cleaning is ultrasonic cleaning. Other components and connections are the same as those in Embodiment 1.
specific Embodiment approach 3
[0027] Embodiment 3: This embodiment is a further description of Embodiment 1, and the solder paste is eutectic alloy solder paste. Other components and connections are the same as those in Embodiment 1.
[0028] The thermal conductivity of the eutectic alloy solder paste is much greater than that of the conductive adhesive and thermal conductive adhesive, which is more conducive to the heat dissipation of the package structure.
PUM
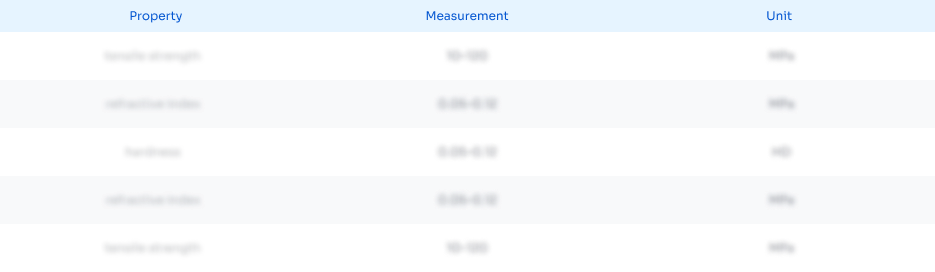
Abstract
Description
Claims
Application Information

- R&D
- Intellectual Property
- Life Sciences
- Materials
- Tech Scout
- Unparalleled Data Quality
- Higher Quality Content
- 60% Fewer Hallucinations
Browse by: Latest US Patents, China's latest patents, Technical Efficacy Thesaurus, Application Domain, Technology Topic, Popular Technical Reports.
© 2025 PatSnap. All rights reserved.Legal|Privacy policy|Modern Slavery Act Transparency Statement|Sitemap|About US| Contact US: help@patsnap.com