Method for preparing atomizing silver tin oxide electrical contactor material containing additives
A technology of electrical contact materials, silver tin oxide, applied in the direction of contacts, circuits, electric switches, etc., can solve the problems of long processing cycle, high production cost, easy agglomeration, etc., to increase the degree of densification, improve the bonding strength, The effect of improving wettability
- Summary
- Abstract
- Description
- Claims
- Application Information
AI Technical Summary
Problems solved by technology
Method used
Image
Examples
Embodiment 1
[0028] 1) According to the preparation of 10kg of Ag-8SnO 2 -3In 2 o 3 -2CeO 2 Ratio of materials Calculate the amount of each raw material, weigh 10kg of pure silver ingot, 0.916kg of pure tin ingot, 0.65kg of indium nitrate, 0.51kg of cerium nitrate, and set aside;
[0029] 2) Take pure silver ingots and pure tin ingots and put them in an intermediate frequency melting furnace to melt into a uniform alloy melt, then atomize them through high-pressure water atomization equipment, dry the obtained powder slurry, and pass through a 200-mesh sieve to obtain silver Tin alloy powder;
[0030]3) Dissolve indium nitrate and cerium nitrate in 3L of water to form an aqueous solution, add 9.33kg of silver-tin alloy powder, and mix the resulting slurry with a low-speed mixer (2h, 30r / min) to obtain nitric acid Silver-tin alloy powder slurry with uniform distribution of indium and cerium nitrate;
[0031] 4) Dry the silver-tin alloy powder slurry evenly distributed indium nitrate an...
Embodiment 2
[0047] 1) First prepare 10kg of Ag-20SnO according to 2 -2La 2 o 3 Calculate the amount of each raw material according to the material ratio, weigh 10kg of pure silver ingot, 2.02kg of pure tin ingot, and 0.535kg of lanthanum nitrate hexahydrate for use;
[0048] 2) Take pure silver ingots and pure tin ingots and place them in an intermediate frequency melting furnace to melt them into a uniform alloy melt, and then atomize them through high-pressure water atomization equipment to obtain silver-tin alloy powder;
[0049] 3) Take lanthanum nitrate and dissolve it with 3L of water to make an aqueous solution, add 9.38kg of silver-tin alloy powder, and use a low-speed mixer to mix the obtained slurry (the time is 1h, and the number of revolutions is 30r / min) to obtain a uniform distribution of lanthanum nitrate silver tin alloy powder paste;
[0050] 4) Dry the silver-tin alloy powder slurry with uniform distribution of lanthanum nitrate at 100°C for 10 hours, crush it with a ...
Embodiment 3
[0054] 1) According to the preparation of 10kg of Ag-10SnO 2 -1.5WO 3 -1ZnO-1.5Mo 2 o 3 Ratio of materials to calculate the amount of each raw material, weigh 10kg of pure silver ingot, 0.916kg of pure tin ingot, 0.156kg of ammonium metatungstate, 0.55kg of zinc nitrate, 0.204kg of ammonium molybdate, and set aside;
[0055] 2) Take pure silver ingots and pure tin ingots and place them in an intermediate frequency melting furnace to melt them into a uniform alloy melt, and then atomize them through high-pressure water atomization equipment to obtain silver-tin alloy powder;
[0056] 3) Dissolve ammonium metatungstate, zinc nitrate, and ammonium molybdate in 2L of water to make an aqueous solution, add 9.39kg of silver-tin alloy powder, and mix the obtained slurry with a low-speed mixer (the time is 0.5h, and the number of revolutions is 20r / min), obtain the silver-tin alloy powder slurry with uniform distribution of ammonium metatungstate, zinc nitrate, and ammonium molybda...
PUM
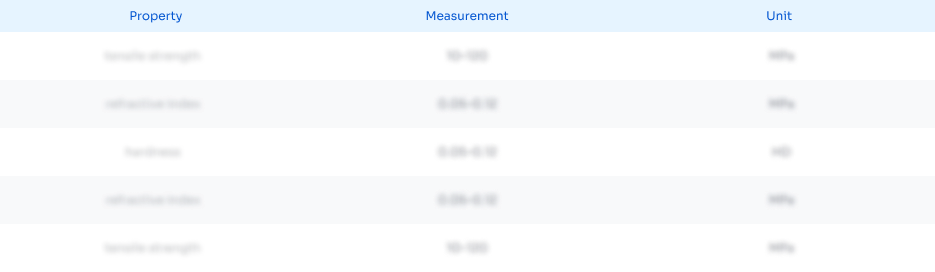
Abstract
Description
Claims
Application Information

- R&D
- Intellectual Property
- Life Sciences
- Materials
- Tech Scout
- Unparalleled Data Quality
- Higher Quality Content
- 60% Fewer Hallucinations
Browse by: Latest US Patents, China's latest patents, Technical Efficacy Thesaurus, Application Domain, Technology Topic, Popular Technical Reports.
© 2025 PatSnap. All rights reserved.Legal|Privacy policy|Modern Slavery Act Transparency Statement|Sitemap|About US| Contact US: help@patsnap.com