Implementing method of high-voltage square-wave generator
A square wave generator and realization method technology, applied in the field of power system, can solve the problems of being susceptible to surrounding electromagnetic interference, limited withstand voltage of mercury-wetting switches, short output pulse width, etc. The effect of strong electromagnetic interference ability and strong load capacity
- Summary
- Abstract
- Description
- Claims
- Application Information
AI Technical Summary
Problems solved by technology
Method used
Image
Examples
Embodiment
[0036] figure 1 The tag description in is:
[0037] V—DC power supply, R a — DC charging resistance, C a — energy storage capacitor, R d —Current limiting damping resistor, I—rising edge circuit, II—falling edge circuit, M 1 — Front MOSFET, M 2 — Rear stage MOSFET, T 1 , T 2 , T 3 ...T n — avalanche triode, R 1 , R 2 , R 3 ...R n — grading resistance, R 11 , R 22 — Damping resistance, point A is the output end of the square wave generator, point B is the high voltage end of the load, and section AB is the high voltage lead.
[0038] figure 2 The tag description in is:
[0039] T 1 —Triggering time of front MOSFET; T 2 —The moment when the front-stage MOSFET is fully turned on; T 3 —The triggering time of the rear-stage MOSFET; T 4 —Avalanche triode trigger time; T 5 —The moment when the avalanche transistor is fully turned on; T 6 —The moment when the rear-stage MOSFET is fully turned on; t 12 —Rising edge time of square wave voltage; t 23 —Square wave...
PUM
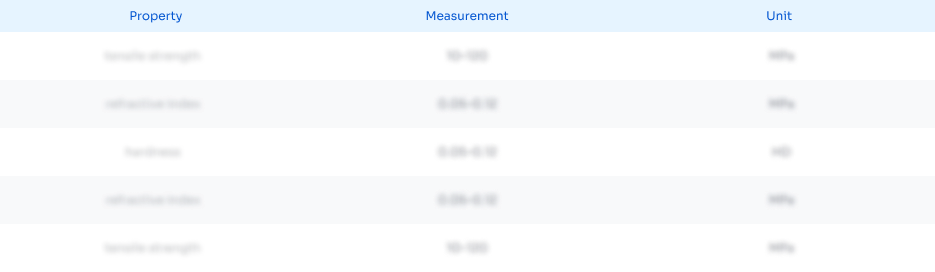
Abstract
Description
Claims
Application Information

- Generate Ideas
- Intellectual Property
- Life Sciences
- Materials
- Tech Scout
- Unparalleled Data Quality
- Higher Quality Content
- 60% Fewer Hallucinations
Browse by: Latest US Patents, China's latest patents, Technical Efficacy Thesaurus, Application Domain, Technology Topic, Popular Technical Reports.
© 2025 PatSnap. All rights reserved.Legal|Privacy policy|Modern Slavery Act Transparency Statement|Sitemap|About US| Contact US: help@patsnap.com