Method adopting laser cladding to form amorphous alloy coating on surface of carbon steel
A technology of laser cladding and amorphous alloy, which is applied to coating metal on the surface of amorphous alloy to improve corrosion resistance. Laser cladding can solve the problems of single coating and poor use effect.
- Summary
- Abstract
- Description
- Claims
- Application Information
AI Technical Summary
Problems solved by technology
Method used
Image
Examples
Embodiment Construction
[0066] The present invention will be further described below in conjunction with accompanying drawing:
[0067] figure 1 As shown, it is the process flow chart of laser cladding amorphous alloy coating on the surface of carbon steel plate, which should be operated in sequence according to the ratio of quantity.
[0068] The amount of chemical substances used in the preparation is determined according to the preset specifications, surface area, alloy layer depth, in grams, milliliters, centimeters 3 , mm is the unit of measurement.
[0069]Surface roughness of carbon steel plate in R a 2.5-5.0μm is appropriate to facilitate the adhesion and curing of the amorphous coating.
[0070] The amorphous coating is based on zirconium nickel aluminum copper according to the atomic number ratio Zr 63.8 Ni 17.2 al 11.4 Cu 7.6 Set, the preset powder thickness is 1mm.
[0071] Solid fusion on the surface of carbon steel plate is the most important process, which must be strictly carr...
PUM
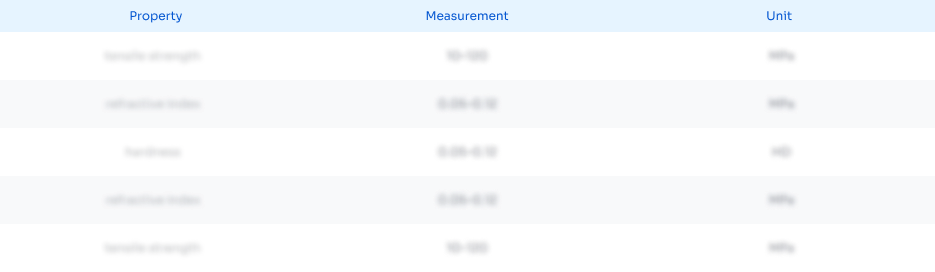
Abstract
Description
Claims
Application Information

- R&D
- Intellectual Property
- Life Sciences
- Materials
- Tech Scout
- Unparalleled Data Quality
- Higher Quality Content
- 60% Fewer Hallucinations
Browse by: Latest US Patents, China's latest patents, Technical Efficacy Thesaurus, Application Domain, Technology Topic, Popular Technical Reports.
© 2025 PatSnap. All rights reserved.Legal|Privacy policy|Modern Slavery Act Transparency Statement|Sitemap|About US| Contact US: help@patsnap.com