Iron adding process-based medium-high silicon molten iron desilication method
A medium-high silicon and molten iron technology, applied in the direction of process efficiency improvement, etc., can solve the problems of difficult slag cleaning, unfavorable maintenance of mixed iron cars, and influence on continuous production, so as to achieve sufficient desiliconization reaction time, low production and operation costs, Efficient desiliconization effect
- Summary
- Abstract
- Description
- Claims
- Application Information
AI Technical Summary
Problems solved by technology
Method used
Examples
Embodiment example 1
[0028] The silicon content of molten iron in a mixing furnace of an enterprise is 0.8%. It is planned to remove the silicon content of the molten iron to 0.2% after mixing the molten iron in the mixing furnace. The mixing rate of the molten iron mixing furnace is 210kg / s. The process is about 6.3 minutes.
[0029] In the process of adding molten iron to the iron mixing furnace, 2-8mm sintered ore is continuously added to the molten iron ladle at a rate of 8kg / s, equivalent to a ton of iron consumption of 38kg / t 铁 , the lime addition rate is 3kg / s, equivalent to a ton of iron consumption is 14kg / t 铁 .
[0030] After the iron has been blended, the ladle is hoisted to the slag removal station with a crane. The slag on the surface of the ladle is dry and easy to remove slag. Tilt the bag seat to quickly remove 80% of the molten iron slag, measure the temperature at 1310°C, and take a sample of the molten iron to detect that the silicon content is 0.15%. After the slag is remove...
Embodiment example 2
[0032] The silicon content of molten iron in a mixing furnace of an enterprise is 1.1%. It is planned to remove the silicon content of the molten iron to 0.3% after mixing the molten iron in the mixing furnace. The mixing rate of the molten iron mixing furnace is 300kg / s. The process is about 6.6 minutes.
[0033] In the process of adding molten iron to the iron mixing furnace, 1-8mm sintered ore is continuously added to the molten iron ladle at a rate of 12kg / s, equivalent to a ton of iron consumption of 40kg / t 铁 , the lime addition rate is 4kg / s, equivalent to a ton of iron consumption is 13kg / t 铁 . During the feeding process, if the slag layer thickens and becomes dry, add 200kg of fluorite.
[0034] After the iron has been blended, the ladle is hoisted to the slag removal station with a crane. The slag on the surface of the ladle is dry and easy to remove slag. Tilt the bag seat to quickly remove 90% of the molten iron slag, measure the temperature at 1350°C, and take a...
PUM
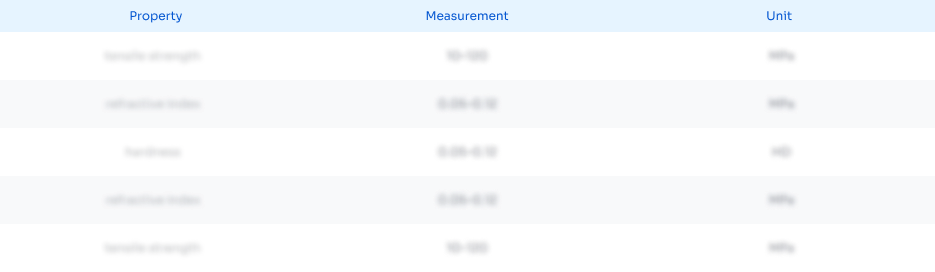
Abstract
Description
Claims
Application Information

- R&D
- Intellectual Property
- Life Sciences
- Materials
- Tech Scout
- Unparalleled Data Quality
- Higher Quality Content
- 60% Fewer Hallucinations
Browse by: Latest US Patents, China's latest patents, Technical Efficacy Thesaurus, Application Domain, Technology Topic, Popular Technical Reports.
© 2025 PatSnap. All rights reserved.Legal|Privacy policy|Modern Slavery Act Transparency Statement|Sitemap|About US| Contact US: help@patsnap.com