Fine wire resistance socket welding method and socket welding mould
A thin wire and resistance technology, applied in resistance welding equipment, resistance electrode holders, manufacturing tools, etc., can solve the problems of mechanical properties that cannot meet the requirements of use, bending strength and toughness, and changes in joint shape, etc., to achieve easy automation, Material saving and good welding quality
- Summary
- Abstract
- Description
- Claims
- Application Information
AI Technical Summary
Problems solved by technology
Method used
Image
Examples
Embodiment Construction
[0042] Specific embodiments of the present invention will be described in detail below in conjunction with the accompanying drawings.
[0043] like figure 1 , figure 2 , image 3 , Figure 4 As shown, a thin wire resistance sleeve welding mold includes an insulating base (6), a copper electrode plate (5), a tantalum electrode plate (4), a thin-walled sleeve (3), and a top cover (7); The insulating base (6) is groove-shaped, one end of the insulating base (6) is provided with a copper electrode plate (5), the other end is provided with a tantalum electrode plate (4), and the top of the insulating base (6) is provided with a top cover ( 7); the thin-walled sleeve (3) passes through the copper electrode plate (5) and the tantalum electrode plate (4); in the space formed by the copper electrode plate (5), the tantalum electrode plate (4) and the top cover Filled with cement to form a cement module (8); the copper electrode plate (5) is provided with conductive screw holes (1...
PUM
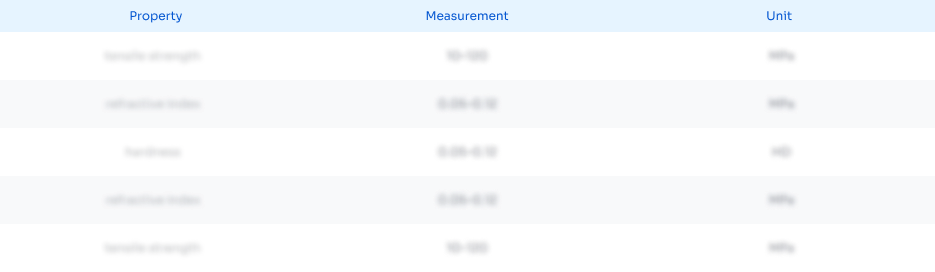
Abstract
Description
Claims
Application Information

- R&D
- Intellectual Property
- Life Sciences
- Materials
- Tech Scout
- Unparalleled Data Quality
- Higher Quality Content
- 60% Fewer Hallucinations
Browse by: Latest US Patents, China's latest patents, Technical Efficacy Thesaurus, Application Domain, Technology Topic, Popular Technical Reports.
© 2025 PatSnap. All rights reserved.Legal|Privacy policy|Modern Slavery Act Transparency Statement|Sitemap|About US| Contact US: help@patsnap.com