A kind of nonionic silicone surfactant and preparation method thereof
A surfactant and silicone technology, applied in chemical instruments and methods, transportation and packaging, dissolution, etc., can solve the problems of high primary hydroxyl end capping rate, low secondary hydroxyl end capping rate, and complex polyether end capping process. , to achieve the effect of easy availability of raw materials and mild reaction conditions
- Summary
- Abstract
- Description
- Claims
- Application Information
AI Technical Summary
Problems solved by technology
Method used
Image
Examples
Embodiment 1
[0033] A) Add 8.0g of methanol, 165g of ethylene oxide and 58g of propylene oxide into the reactor, and react for 4 hours in the presence of 1.1g of KOH catalyst, pressure ≤ 0.4MPa, and reaction temperature of 110°C to obtain monofunctional polymer Ether (I);
[0034] B) 8.0g of acrylic acid and 103g of the above-mentioned monofunctional polyether (I) were reacted at 210°C for 3 hours under the condition of 0.1% sulfuric acid catalyst to obtain a double bond-containing polyether ester (II);
[0035]C) React octamethylcyclotetrasiloxane, hydrogen-containing silicone oil and tetramethyldisiloxane under the action of sulfuric acid at 80°C for 5 hours to obtain polysiloxane (III), in which octamethylcyclotetrasiloxane The molar ratio between oxane, hydrogen-containing silicone oil (1.58% hydrogen content) and tetramethyldisiloxane is 10:0.11:1;
[0036] D) Add 120g of polyether ester (II) and 67g of polysiloxane (III) obtained by the above two-step reaction into the reactor, heat...
Embodiment 2
[0041] A) Add 46g of ethanol and 792g of ethylene oxide into the reactor, and react for 4 hours in the presence of 4.0g of KOH catalyst, pressure ≤ 0.4MPa, and reaction temperature of 110°C to obtain monofunctional polyether (I);
[0042] B) 40.0g of oleic acid and 120g of the above-mentioned monofunctional polyether (I) were reacted at 210°C for 3 hours under the condition of 0.1% monobutyltin oxide catalyst to obtain the polyether ester (II) containing double bonds;
[0043] C) React octamethylcyclotetrasiloxane, hydrogen-containing silicone oil and hexamethyldisiloxane under the action of sulfuric acid at 80°C for 5 hours to obtain polysiloxane (III), in which octamethylcyclotetrasiloxane The molar ratio between oxane, hydrogen-containing silicone oil (1.59% hydrogen content) and hexamethyldisiloxane is 8:0.11:1;
[0044] D) Add 112g of polyether ester (II) and 68g of polysiloxane (III) obtained by the above two-step reaction into the reactor, heat up to 60-120°C for 7 hour...
Embodiment 3
[0049] A) Add 9.8g of n-butanol, 330g of ethylene oxide, and 96g of propylene oxide into the reactor, and react for 4 hours in the presence of 1.5g of KOH catalyst, pressure ≤ 0.4MPa, and reaction temperature of 110°C to obtain monofunctional Polyether (I);
[0050] B) 20.0g of 10-undecylenic acid methyl ester and 265g of the above monofunctional polyether (I) were reacted at 200°C for 3 hours under the condition of 0.1% dibutyltin oxide catalyst to obtain a double bond-containing polyether ester (II);
[0051] C) React octamethylcyclotetrasiloxane and tetramethyldisiloxane under the action of sulfuric acid at 80°C for 5 hours to obtain polysiloxane (III), in which octamethylcyclotetrasiloxane and tetramethyldisiloxane The mol ratio between methyldisiloxane is 5:1;
[0052] D) Add 282g of polyether ester (II) and 80g of polysiloxane (III) obtained from the above two-step reaction into the reactor, heat it up to 60-120°C under normal pressure with 20ppm Pt catalyst and 70g of...
PUM
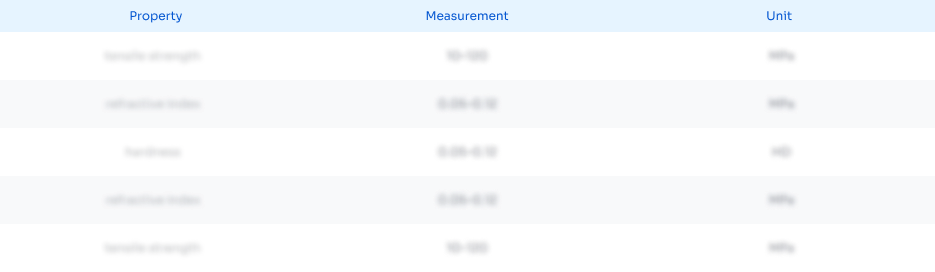
Abstract
Description
Claims
Application Information

- R&D
- Intellectual Property
- Life Sciences
- Materials
- Tech Scout
- Unparalleled Data Quality
- Higher Quality Content
- 60% Fewer Hallucinations
Browse by: Latest US Patents, China's latest patents, Technical Efficacy Thesaurus, Application Domain, Technology Topic, Popular Technical Reports.
© 2025 PatSnap. All rights reserved.Legal|Privacy policy|Modern Slavery Act Transparency Statement|Sitemap|About US| Contact US: help@patsnap.com