Wheel steel applicable to railway wagon and wheel preparation method
A railway locomotive and wheel steel technology, applied in the direction of manufacturing tools, heat treatment equipment, furnaces, etc., can solve problems such as abnormal wheel flange wear, abnormal tread wear, tread peeling, etc., and achieve good results in actual operation
- Summary
- Abstract
- Description
- Claims
- Application Information
AI Technical Summary
Problems solved by technology
Method used
Image
Examples
Embodiment 1
[0026] The molten steel whose chemical composition is shown in Example 1 in Table 1 is formed through converter steelmaking process, LF furnace refining process, VD vacuum treatment process, round billet continuous casting process, ingot cutting and rolling process, heat treatment process, processing, and finished product inspection process. The comparative example is a locomotive wheel imported from abroad. Example 1 is carried out according to the heat treatment scheme proposed by the present invention. The heat treatment process is as follows: the temperature is raised to 880°C with the furnace, and the temperature is kept at 880°C for 3.5 hours. The wheel is heated to 860°C with the furnace, and after 4 hours of heat preservation, it is cooled by spraying water through the inclined nozzle for 400 seconds, and then it is kept at 480°C for 5 hours, and then it is air-cooled.
[0027] The mechanical properties of the rim are shown in Table 2, and it can be seen from Table 2 th...
Embodiment 2
[0029] The molten steel whose chemical composition is shown in Example 2 of Table 1 is formed through converter steelmaking process, LF furnace refining process, VD vacuum treatment process, round billet continuous casting process, ingot cutting and rolling process, heat treatment process, processing, and finished product inspection process. The comparative example is a locomotive wheel imported from abroad. Example 2 is carried out according to the heat treatment scheme proposed by the present invention. The heat treatment process is as follows: heat up to 870°C with the furnace, heat it at 870°C for 3 hours, and then take it out of the furnace and air cool it to room temperature about 20°C. The wheel is heated to 855°C with the furnace, and after 4 hours of heat preservation, it is cooled by spraying water with inclined nozzles for 400 seconds, and then kept at 500°C for 5 hours, and then air-cooled.
[0030] The mechanical properties of the rim are shown in Table 2. It can b...
PUM
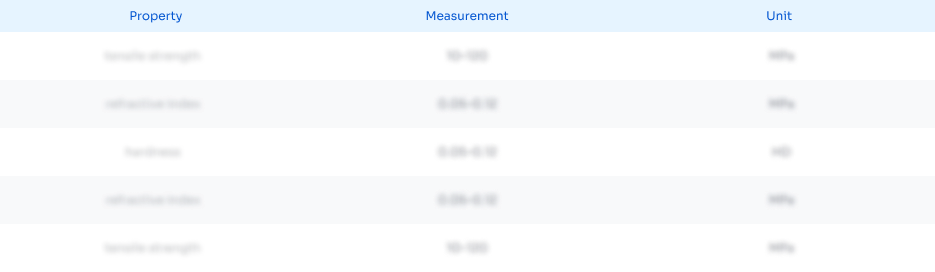
Abstract
Description
Claims
Application Information

- R&D Engineer
- R&D Manager
- IP Professional
- Industry Leading Data Capabilities
- Powerful AI technology
- Patent DNA Extraction
Browse by: Latest US Patents, China's latest patents, Technical Efficacy Thesaurus, Application Domain, Technology Topic, Popular Technical Reports.
© 2024 PatSnap. All rights reserved.Legal|Privacy policy|Modern Slavery Act Transparency Statement|Sitemap|About US| Contact US: help@patsnap.com