Epoxy resin curing agent and preparation method thereof
An epoxy resin curing and solvent technology, applied in the field of epoxy resin curing agent and its preparation, can solve the problems of poor dispersion and compatibility of additives, reduce the mechanical properties of epoxy resin, etc., achieve high synergistic flame retardancy, avoid The effect of poor matrix compatibility and simple preparation process
- Summary
- Abstract
- Description
- Claims
- Application Information
AI Technical Summary
Problems solved by technology
Method used
Image
Examples
Embodiment 1
[0030] The synthesis of epoxy resin curing agent is realized through the following steps:
[0031] (1) In a 100mL three-neck flask equipped with a magnetic rotor stirring, a condenser, and a thermometer, dissolve hexachlorocyclotriphosphazene (6.94g, 0.02mol) prepared by multiple sublimation in 50mL of tetrahydrofuran (THF) solvent, drop Add the prepared (9.28g, 0.08mol) THF solution of sodium phenate, and react at 40°C for 12 hours under nitrogen protection; remove THF by rotary distillation, wash with deionized water several times, and vacuum dry at 50°C for 24 hours. A milky white colloid is obtained. Among them, the preparation method of sodium phenate is: under the protection of nitrogen, (1.84g, 0.08mol) metal sodium and (7.52g, 0.08mol) phenol are reacted in 50mL THF solution at 25°C for 2 hours.
[0032] (2) Dissolve (4.36g, 0.04mol) p-aminophenol in 50mL tetrahydrofuran (THF) solvent in a 100mL three-neck flask equipped with magnetic rotor stirring, condenser and the...
Embodiment 2
[0035] The synthesis of epoxy resin curing agent is realized through the following steps:
[0036] (1) In a 100mL three-neck flask equipped with a magnetic rotor stirring, a condenser, and a thermometer, dissolve hexachlorocyclotriphosphazene (3.47g, 0.01mol) prepared by multiple sublimation in 50mL of tetrahydrofuran (THF) solvent, drop Add the prepared (4.64g, 0.04mol) sodium phenoxide THF solution, and react at 40°C for 12 hours under nitrogen protection; remove THF by rotary distillation, wash with deionized water several times, and vacuum dry at 50°C for 24 hours to obtain Milky white colloid. Among them, the preparation method of sodium phenate is: under the protection of nitrogen, (0.92g0.04mol) metal sodium and (3.76g0.04mol) phenol are reacted in 50mL THF solution at 25°C for 2 hours.
[0037] (2) Dissolve (2.18g, 0.02mol) p-aminophenol in 50mL tetrahydrofuran (THF) solvent in a 100mL three-necked flask equipped with magnetic rotor stirring, condenser and thermometer...
Embodiment 3
[0040] The synthesis of epoxy resin curing agent is realized through the following steps:
[0041] (1) In a 100mL three-neck flask equipped with a magnetic rotor stirring, a condenser, and a thermometer, dissolve hexachlorocyclotriphosphazene (34.70g, 0.10mol) prepared by multiple sublimation in 50mL of tetrahydrofuran (THF) solvent, drop Add the prepared (46.40g, 0.40mol) sodium phenoxide THF solution, and react at 40°C for 12 hours under nitrogen protection; remove THF by rotary distillation, wash with deionized water several times, and vacuum dry at 50°C for 24 hours to obtain Milky white colloid. Among them, the preparation method of sodium phenate is: under the protection of nitrogen, (9.20g0.40mol) metallic sodium and (37.60g0.40mol) are reacted in 50mL THF solution at 25°C for 2 hours.
[0042] (2) Dissolve (21.80g, 0.20mol) p-aminophenol in 50mL tetrahydrofuran (THF) solvent in a 100mL three-necked flask equipped with magnetic rotor stirring, condenser and thermometer...
PUM
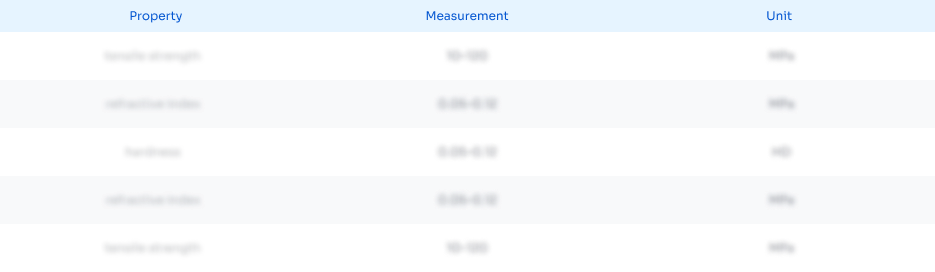
Abstract
Description
Claims
Application Information

- Generate Ideas
- Intellectual Property
- Life Sciences
- Materials
- Tech Scout
- Unparalleled Data Quality
- Higher Quality Content
- 60% Fewer Hallucinations
Browse by: Latest US Patents, China's latest patents, Technical Efficacy Thesaurus, Application Domain, Technology Topic, Popular Technical Reports.
© 2025 PatSnap. All rights reserved.Legal|Privacy policy|Modern Slavery Act Transparency Statement|Sitemap|About US| Contact US: help@patsnap.com