High-interface-bonding-firmness carbon fiber/carbon nanotube composite material and preparation technique thereof
A carbon nanotube and interface bonding technology, which is applied in the field of nanomaterials, can solve the problems of difficult uniform dispersion, easy agglomeration, and high surface energy of carbon nanotubes, achieves increased interface strength, simple and easy preparation method, and good interlayer The effect of shear strength
- Summary
- Abstract
- Description
- Claims
- Application Information
AI Technical Summary
Problems solved by technology
Method used
Examples
Embodiment 1
[0029] Multi-walled carbon nanotubes (OD<8nm) and carbon fibers prepared by chemical vapor deposition were used as the initial raw materials. Nanotubes and m-phenylene bismaleimide undergo Michael addition reaction to obtain multi-walled carbon nanotubes with m-phenylene bismaleimide on the surface, and then combine them with aminated carbon fiber cloth in a certain amount. Composite by means of multi-dimensional hybrid composite materials containing carbon fiber / carbon nanotube / bismaleimide resin.
[0030]Step (1): In a 250mL single-necked round-bottomed flask equipped with a stirrer, add 1.1g of dried multi-walled carbon nanotube raw material and 100mL, 30% nitric acid solution, treat it under 100kHz ultrasonic waves for 20 hours, and then heat to 30°C, reacted for 40 hours, filtered with poly(tetrafluoroethylene) microfiltration membrane with a pore size of 0.8 μm, washed with deionized water for 4-10 times until neutral, and vacuum dried at 30°C for 48 hours to obtain the ...
Embodiment 2
[0038] Double-walled carbon nanotubes (OD<8nm) prepared by solar energy method were used as the initial raw material. Phenyl ether type bismaleimide undergoes Michael addition reaction to obtain double-walled carbon nanotubes with diphenyl ether type bismaleimide attached to the surface, and then compound them with aminated carbon fibers in a certain way. A multidimensional hybrid composite material containing carbon fiber / carbon nanotube / bismaleimide resin was obtained.
[0039] Step (1): in the 500mL single-neck round bottom flask that magnetic stirring rotor has been housed, add 1.1g double-walled carbon nanotube raw material, the sulfuric acid of 100mL, 50% weight concentration, with 10 3 Treat at the speed of r / min for 30 hours, then heat to 150°C, react for 50 hours, filter with polytetrafluoroethylene microfiltration membrane with a pore size of 0.8 μm, wash repeatedly with deionized water until neutral, and vacuum dry at 100°C After 36 hours, the purified carbon nanot...
PUM
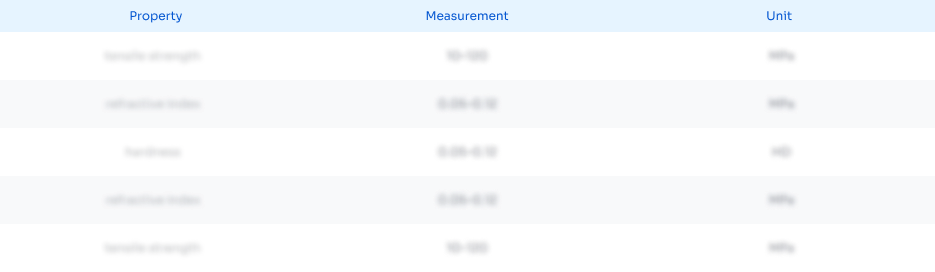
Abstract
Description
Claims
Application Information

- R&D
- Intellectual Property
- Life Sciences
- Materials
- Tech Scout
- Unparalleled Data Quality
- Higher Quality Content
- 60% Fewer Hallucinations
Browse by: Latest US Patents, China's latest patents, Technical Efficacy Thesaurus, Application Domain, Technology Topic, Popular Technical Reports.
© 2025 PatSnap. All rights reserved.Legal|Privacy policy|Modern Slavery Act Transparency Statement|Sitemap|About US| Contact US: help@patsnap.com