Method for preparing yttrium aluminium garnet transparent ceramic with composite structure
A technology of yttrium aluminum garnet and composite structure is applied in the field of preparation of Re:YAG composite structure polycrystalline transparent ceramics
- Summary
- Abstract
- Description
- Claims
- Application Information
AI Technical Summary
Problems solved by technology
Method used
Image
Examples
Embodiment 1
[0033] Weigh 100g of high-purity Nd:YAG nanopowder and YAG nanopowder (doping amount of 1at% Nd), respectively dissolve them in 200 ethanol solution, add 0.5wt% ammonium polymethacrylate dispersant, 0.5wt % Sintering aid TEOS, according to the material: ball: water=1:5:3 ratio of ball milling, using nylon ball and nylon tank to mix ball milling for 60 hours, ball milling speed 300r / min; pour the ball milled slurry into 15μm aperture Ultrasonic filtration is performed in the sample, 5MHz ultrasonic frequency is selected, 80% output ultrasonic power, 10 seconds off every 1 minute of ultrasonic, intermittent ultrasonic, ultrasonic for a total of 10 minutes; take the sieved suspended solid slurry, dry in an oven at 90 ℃, and the powder After crushing and debinding at 700°C under oxygen atmosphere for 5 hours, the sorted powder is obtained. Weigh 50g of the separated Nd: YAG nano powder and 20g YAG nano powder, and add 0.8wt% dispersant ammonium polyacrylate, 0.3wt% binder polyvinyl...
Embodiment 2
[0035] Weigh the commercially available high-purity powder Y according to the stoichiometric ratio 2 O 3 :39.8328g, Al 2 O 3 :30.585g, Nd 2 O 3 :1.2114g (2at%Nd doping amount), Sm 2 O 3 :(2at% Sm doping amount) add 0.2wt% MgO sintering aid, 0.5wt% dispersant polyacrylic acid (PAA), 0.2wt% binder carboxymethyl cellulose (CMC), 0.5wt% increase Plasticizer PEG-400, 0.5wt% defoaming agent n-butanol; pour raw materials, grinding balls, and ball mill additives into 150 grams of deionized water and ball mill and mix for 24 hours, ball mill speed 350r / m, material: ball = 1:5. Put the ball mill mixed slurry into a vacuum tank, and stir for 30 minutes with a vacuum degree of -0.1pa or less, until no bubbles escape in the slurry; Nd 2 O 3 The doped and defoamed slurry is injected into the center of the gypsum mold. After the gypsum mold is finished, remove the frame and inject Sm into the outer ring 2 O 3 The doped slurry, wait for the green body to shrink and separate the gypsum mold, and ...
Embodiment 3
[0044] Weigh three parts of high purity powder Y according to the stoichiometric ratio 2 O 3 :39.8328g, Al 2 O 3 :30.585g, Nd 2 O 3 :0.6057g (1at% Nd doping amount), add 0.2wt% MgO sintering aid, Cr 2 O 3 : (0.5at% Cr doping), add 0.25wt% CaO sintering aid, 0.5wt% dispersant polycarboxylic acid, 0.25wt% binder methyl cellulose (MC), 0.5wt% plasticization PEG-2000, 1wt% defoamer methanol; pour the raw materials, grinding balls, and ball mill additives into 150 g of deionized water and ball mill and mix for 24 hours, the ball mill speed is 350r / m, material: ball=1:5; after mixing the ball mill Put the slurry into a vacuum tank and stir for 30 minutes until no bubbles escape in the slurry. The long strip of gypsum mold is divided into three or five sections with plastic partitions and injected into pure
[0045] YAG slurry, Nd 2 O 3 Doped paste, Cr 2 O 3 The slurry is doped, after the gypsum mold is finished absorbing the slurry, the partitions are removed and the slurry is used to f...
PUM
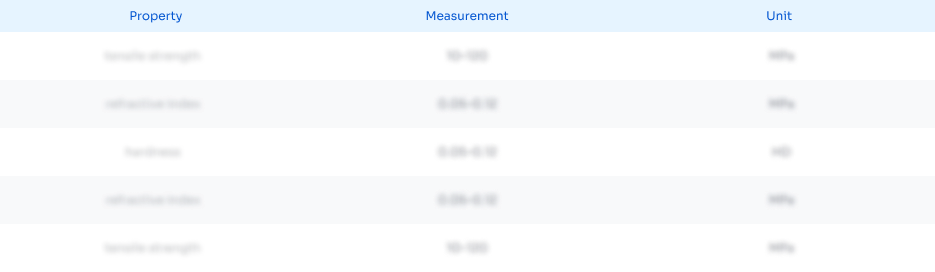
Abstract
Description
Claims
Application Information

- R&D
- Intellectual Property
- Life Sciences
- Materials
- Tech Scout
- Unparalleled Data Quality
- Higher Quality Content
- 60% Fewer Hallucinations
Browse by: Latest US Patents, China's latest patents, Technical Efficacy Thesaurus, Application Domain, Technology Topic, Popular Technical Reports.
© 2025 PatSnap. All rights reserved.Legal|Privacy policy|Modern Slavery Act Transparency Statement|Sitemap|About US| Contact US: help@patsnap.com