Calcium treatment method under special steelmaking process
A calcium treatment and process technology, applied in the direction of improving process efficiency, etc., can solve problems such as lack of quality, and achieve the effects of improving purity, obvious economic benefits, and stable calcium yield
- Summary
- Abstract
- Description
- Claims
- Application Information
AI Technical Summary
Problems solved by technology
Method used
Examples
Embodiment example 1
[0017] This example provides a calcium treatment method under a special steelmaking process, which mainly adopts deep desulfurization of molten iron pretreatment, oxygen control at the end point of converter, rapid white slag production in LF furnace and process aluminum control, quartz sand adjustment of alkalinity and slag at the end point of ladle Measures such as fluidity, RH low vacuum long-term degassing treatment, secondary LF temperature-adjusting slag calcium treatment, prolonging the soft blowing time before and after calcium treatment, and continuous casting process protection pouring have improved the purity of molten steel and the pass rate of steel plate flaw detection. The yield rate of calcium is guaranteed, and the effect of calcium treatment is improved.
[0018] In this example, the hot metal is pretreated for desulfurization, and CaO+Mg powder is injected to remove the sulfur content of the hot metal to 0.0020%, and the slagging treatment is carried out; the...
PUM
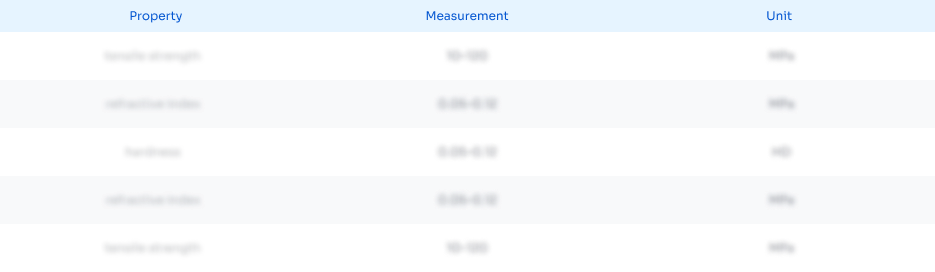
Abstract
Description
Claims
Application Information

- R&D
- Intellectual Property
- Life Sciences
- Materials
- Tech Scout
- Unparalleled Data Quality
- Higher Quality Content
- 60% Fewer Hallucinations
Browse by: Latest US Patents, China's latest patents, Technical Efficacy Thesaurus, Application Domain, Technology Topic, Popular Technical Reports.
© 2025 PatSnap. All rights reserved.Legal|Privacy policy|Modern Slavery Act Transparency Statement|Sitemap|About US| Contact US: help@patsnap.com